Antibacterial wood plastic composite preparation method through gamma rays
A wood-plastic composite material and gamma ray technology are applied in the field of preparing antibacterial wood-plastic composite materials by using gamma rays, which can solve problems such as poor anti-corrosion and anti-bacterial properties, and achieve the effects of stable product quality, uniform mixing and easy removal.
- Summary
- Abstract
- Description
- Claims
- Application Information
AI Technical Summary
Problems solved by technology
Method used
Image
Examples
specific Embodiment approach 1
[0017] Embodiment 1: A method for preparing antibacterial wood-plastic composite materials using gamma rays in this embodiment is carried out according to the following steps:
[0018] 1. The AgNO 3 Dissolve in deionized water and stir until AgNO 3 Dissolve completely, then add ammonia water at a rate of 10 drops / min to 20 drops / min until the precipitate completely disappears, then stir for 8 minutes to 15 minutes at a stirring speed of 50r / min to 500r / min, then add wood powder and isopropanol, and ultrasonically disperse for 1h to 3h under the condition of ultrasonic frequency of 50kHz to 60kHz to obtain a wood flour mixture;
[0019] The AgNO 3 The ratio of the mass to the volume of deionized water is 2.2g: (90-110) mL; the AgNO 3 The mass ratio to wood powder is 1: (1-10); the AgNO 3 The ratio of the mass of isopropanol to the volume of isopropanol is 2.2g: (25-35)mL;
[0020] Two, pass into nitrogen in the wood flour mixed solution that step one obtains, then in 60 I...
specific Embodiment approach 2
[0023] Specific embodiment two: the difference between this embodiment and specific embodiment one is: in step one, ammonia water is then added at a rate of 15 drops / min until the precipitate produced completely disappears. Other steps and parameters are the same as those in the first embodiment.
specific Embodiment approach 3
[0024] Embodiment 3: The difference between this embodiment and Embodiment 1 or 2 is that in step 1, wood flour and isopropanol are then added, and ultrasonically dispersed for 1 hour at an ultrasonic frequency of 53 kHz. Other steps and parameters are the same as those in Embodiment 1 or 2.
PUM
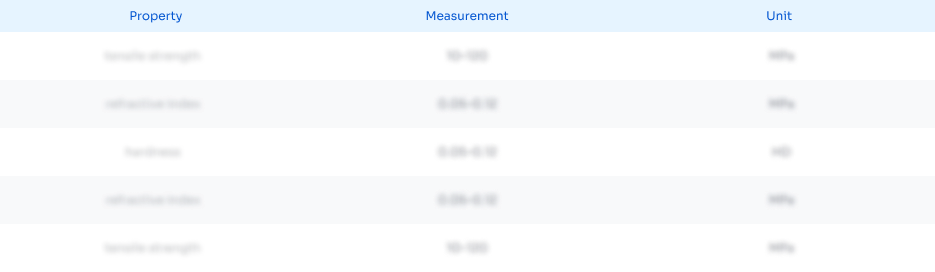
Abstract
Description
Claims
Application Information

- Generate Ideas
- Intellectual Property
- Life Sciences
- Materials
- Tech Scout
- Unparalleled Data Quality
- Higher Quality Content
- 60% Fewer Hallucinations
Browse by: Latest US Patents, China's latest patents, Technical Efficacy Thesaurus, Application Domain, Technology Topic, Popular Technical Reports.
© 2025 PatSnap. All rights reserved.Legal|Privacy policy|Modern Slavery Act Transparency Statement|Sitemap|About US| Contact US: help@patsnap.com