Preparation method for continuous fibre fabric-reinforced anionic polyamide 6 composite material and composite material
A continuous fiber and composite material technology, applied in the field of composite materials, can solve the problems of many processes, low carbon fiber content, and limited application, and achieve the effects of increasing the degree of polymerization reaction, increasing fiber volume content, and improving mechanical properties
- Summary
- Abstract
- Description
- Claims
- Application Information
AI Technical Summary
Problems solved by technology
Method used
Image
Examples
preparation example Construction
[0032] The preparation method of the continuous fiber fabric reinforced anionic polyamide 6 composite material of the present invention specifically comprises the following steps:
[0033] (1) Place the continuous fiber fabric in an oven at 200-400°C, heat and dry it with inert gas for 2-4 hours, then lay it in a composite mold, and preheat it in an oven or a hot press. The inert gas introduced is at least one of nitrogen, argon or helium.
[0034] (2) Heat the caprolactam monomer in a reaction vessel to 110-130°C to melt the material, add an initiator after vacuum dehydration for 0.5-1 hour, and continue vacuum dehydration for 0.5-1 hour;
[0035] (3) After releasing the vacuum, add the catalyst into the reaction vessel to disperse for 1 to 8 minutes, use the liquid molding method to pump the reaction solution into the composite material mold that has been laid with continuous fiber fabric and preheated to 150 to 180°C, and keep warm for 0.5 After ~1 hour, the mold is demoul...
Embodiment 1
[0048] Place 45 parts by mass of continuous quartz fiber three-dimensional fabrics in a 200°C oven fed with nitrogen to dry for 4 hours, then lay them on a composite material mold and preheat them to 150°C, then add 100 parts by mass of caprolactam monomer to a 1L reactor, and heat up to Melt at 110°C, add 0.1 parts by mass of sodium hydroxide after vacuum dehydration for 0.5 hours, continue vacuum dehydration for 0.5 hours, then add 0.3 parts by mass of toluene 2,4 diisocyanate, stir for 8 minutes and quickly inject the reaction solution into the already Preheat to 150° C. in a mold (pressure 0.1 MPa), demould after 0.5 hour to obtain continuous glass fiber fabric reinforced anionic polyamide 6 composite material (fiber weight fraction 30%). The typical properties of the composite materials are shown in Table 1.
Embodiment 2
[0050] Arrange 50 parts by mass of continuous carbon fiber plain weave into a 400°C oven filled with nitrogen and dry for 2 hours, then lay it on the composite material mold and preheat it to 160°C, then add 100 parts by mass of caprolactam monomer into a 1L reactor and heat up to 120°C After melting and vacuum dehydration for 0.5 hours, add 0.3 parts by mass of sodium methoxide, continue vacuum dehydration for 0.5 hours, then add 0.6 parts by mass of toluene 2,4 diisocyanate, stir for 3 minutes and quickly inject the reaction solution into the preheated to In a mold at 160° C. (pressure 0.3 MPa), demould after 0.5 hour to obtain a continuous carbon fiber fabric reinforced anionic polyamide 6 composite material (fiber weight fraction 50%). The typical properties of the composite materials are shown in Table 1.
PUM
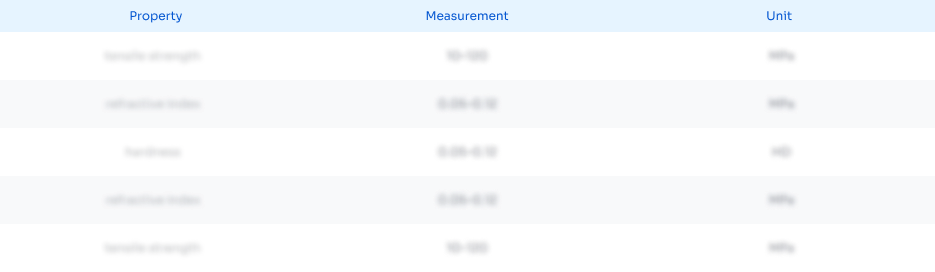
Abstract
Description
Claims
Application Information

- R&D
- Intellectual Property
- Life Sciences
- Materials
- Tech Scout
- Unparalleled Data Quality
- Higher Quality Content
- 60% Fewer Hallucinations
Browse by: Latest US Patents, China's latest patents, Technical Efficacy Thesaurus, Application Domain, Technology Topic, Popular Technical Reports.
© 2025 PatSnap. All rights reserved.Legal|Privacy policy|Modern Slavery Act Transparency Statement|Sitemap|About US| Contact US: help@patsnap.com