Preparation method of cellulose triacetate ester film
A technology of cellulose triacetate and ester film, applied in flat products, applications, coatings, etc., can solve the problems of apparent quality influence, crystal point defects, affecting optical properties, etc., to improve uniformity and solve crystal point problems , the effect of improving the appearance and optical properties
- Summary
- Abstract
- Description
- Claims
- Application Information
AI Technical Summary
Problems solved by technology
Method used
Image
Examples
preparation example Construction
[0037] The preparation method of cellulose triacetate film of the present invention is:
[0038] 1. Drying treatment of cellulose triacetate
[0039] The raw material cellulose triacetate with a moisture content of 1%-3% is heated and dried at a wind temperature of 50-130°C, and the moisture content of the treated cellulose triacetate is ≤0.3% by weight.
[0040] 2. Methanol rewetting of cellulose triacetate
[0041] The cellulose triacetate treated in step 1 enters the methanol vapor, and the cellulose triacetate treated in step 1 is rehumidified in the methanol vapor, so that the methanol content of the treated cellulose triacetate reaches 0.1 -2% by weight.
[0042] 3. Preparation of cellulose triacetate cotton glue solution
[0043] The preparation process of the cellulose triacetate cotton glue of the present invention is the same as that of the existing cellulose triacetate cotton glue, including four steps of feeding, mixing and dissolving, filtering and standing at ...
Embodiment 1
[0062] 1. Drying treatment of cellulose triacetate
[0063] The cellulose triacetate with a moisture content of 2.0% is dried in the drying device 7 .
[0064] Air temperature 50 ℃ in drying device 7.
[0065] The water content of the treated cellulose triacetate was 0.3% by weight.
[0066] 2. Methanol rewetting of cellulose triacetate
[0067] The cellulose triacetate treated in step 1 is rehumidified in the cellulose triacetate methanol rehumidification device 8, so that the methanol content of the treated cellulose triacetate is 2% (by weight).
[0068] 3. Dissolution of cellulose triacetate
[0069] Add the cellulose triacetate treated in step 2 into the dissolving device 1 containing the main solvent, co-solvent and plasticizer for 5 hours to fully dissolve to prepare a uniform cotton glue solution. Test the dissolution quality of the cotton glue solution.
[0070] 4. Tape casting of cellulose triacetate film
[0071] After the cotton glue liquid obtained in proces...
Embodiment 2
[0073] 1. Drying treatment of cellulose triacetate
[0074] The cellulose triacetate with a moisture content of 2.0% is dried in the drying device 7 .
[0075] Air temperature in drying device 7 is 130°C.
[0076] The moisture content of the treated cellulose triacetate was 0.
[0077] 2. Methanol rewetting of cellulose triacetate
[0078] The cellulose triacetate treated in step 1 is rehumidified in the cellulose triacetate methanol rehumidification device 8, so that the methanol content of the treated cellulose triacetate is 1% by weight.
[0079] 3. Dissolution of cellulose triacetate
[0080] Add the cellulose triacetate treated in step 2 into the dissolving device 1 containing the main solvent, co-solvent and plasticizer for 5 hours to fully dissolve to prepare a uniform cotton glue solution. Test the dissolution quality of the cotton glue solution.
[0081] 4. Tape casting of cellulose triacetate film
[0082] After the cotton glue liquid obtained in process 3 is f...
PUM
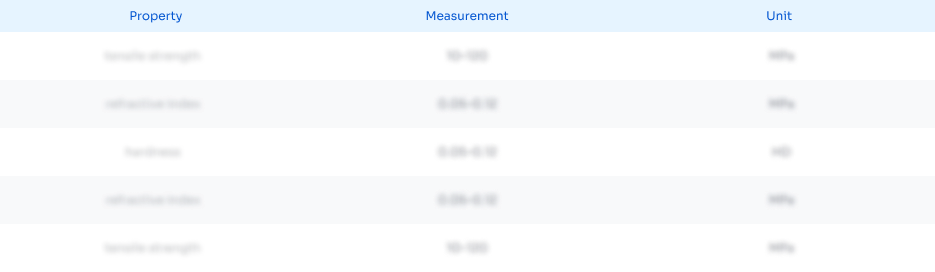
Abstract
Description
Claims
Application Information

- R&D Engineer
- R&D Manager
- IP Professional
- Industry Leading Data Capabilities
- Powerful AI technology
- Patent DNA Extraction
Browse by: Latest US Patents, China's latest patents, Technical Efficacy Thesaurus, Application Domain, Technology Topic, Popular Technical Reports.
© 2024 PatSnap. All rights reserved.Legal|Privacy policy|Modern Slavery Act Transparency Statement|Sitemap|About US| Contact US: help@patsnap.com