In-situ carbon and oxide doping of atomic layer deposition silicon nitride films
A technology of silicon carbonitride and silicon carbonitride, which is applied in the field of thin film deposition, can solve the problems of electrical performance degradation, low yield, low cleaning and etching rate, etc.
- Summary
- Abstract
- Description
- Claims
- Application Information
AI Technical Summary
Problems solved by technology
Method used
Image
Examples
Embodiment Construction
[0014] Embodiments disclosed herein relate generally to processing of substrates, and more specifically, to methods for forming dielectric films. In one embodiment, the method includes placing a plurality of substrates inside a processing chamber, and performing the sequence of exposing the substrates to a first reactive gas comprising silicon, and then exposing the substrates to exposing the substrate to a plasma of a second reactive gas comprising at least one of nitrogen and oxygen or carbon, and repeating the sequence to form silicon carbonitride or silicon oxycarbonitride on each of the substrates the dielectric film.
[0015] figure 1 is a cross-sectional side view of a processing chamber 100 according to one embodiment. The processing chamber 100 is capable of performing one or more deposition processes on one or more substrates 60 . The processing chamber 100 includes a gas / plasma distribution assembly 30 capable of distributing one or more gases and / or plasma acros...
PUM
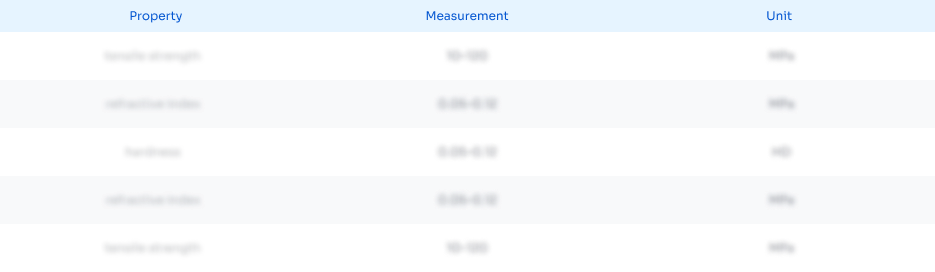
Abstract
Description
Claims
Application Information

- R&D
- Intellectual Property
- Life Sciences
- Materials
- Tech Scout
- Unparalleled Data Quality
- Higher Quality Content
- 60% Fewer Hallucinations
Browse by: Latest US Patents, China's latest patents, Technical Efficacy Thesaurus, Application Domain, Technology Topic, Popular Technical Reports.
© 2025 PatSnap. All rights reserved.Legal|Privacy policy|Modern Slavery Act Transparency Statement|Sitemap|About US| Contact US: help@patsnap.com