Fiber sizing agent having catalytic function and process for preparing fiber structure by adopting same
A process method and fiber structure technology, applied in fiber processing, textiles and papermaking, etc., can solve problems such as low efficiency, poor quality, cost waste, etc., and achieve the effects of uniform distribution, less waste, and reduced production processes
- Summary
- Abstract
- Description
- Claims
- Application Information
AI Technical Summary
Problems solved by technology
Method used
Image
Examples
Embodiment 1
[0041] Prepare 100kg of fiber sizing agent: add 20kg of resin film former, 2kg of lubricant, 0.5kg of antistatic agent, 0.3kg of silane coupling agent, 76.7kg of deionized water, 0.5kg of composite high temperature catalyst in sequence. After stirring evenly, add it to the oiler for drawing fiber filaments. Then, the fiber filaments were dried, twisted, twisted, and woven in the same process to make filter cloth, and filled into the reaction vessel for experimental testing. The reaction temperature was 280°C. Use gas chromatography to test the chromatographic peak integrated area of chlorobenzene in the sample to reflect the change in the amount and concentration of chlorobenzene.
[0042] According to the process method described in this embodiment, from configuring the sizing agent, drawing the fiber filament to obtaining the final product, the entire process time takes about 5 hours, and the transfer process usually takes 20 hours. It can be seen that the composite high temp...
Embodiment 2
[0044] To prepare 100 kg fiber sizing agent: add 20 kg of resin film former, 2 kg of lubricant, 0.5 kg of antistatic agent, 0.3 kg of silane coupling agent, 76.84 kg of deionized water, and 0.3 kg of composite photocatalyst. After stirring evenly, add it to the oiler for drawing fiber filaments. Then, the fiber filaments are dried, twisted, twisted, and woven in the same process to make filter cloth, and filled into the reaction vessel for experimental testing. Use gas chromatography to test the integrated area of the chromatographic peak of formaldehyde in the sample to reflect the change in the amount and concentration of formaldehyde.
[0045] According to the process method described in this embodiment, from configuring the sizing agent, drawing the fiber filament to obtaining the final product, the entire process time is also about 5 hours, and the transfer process usually takes 20 hours. It can be seen that the composite photocatalyst and the ordinary fiber After the siz...
Embodiment 3
[0047] Prepare 100kg of fiber sizing agent: add 20kg of resin film-forming agent, 2kg of lubricant, 0.5kg of antistatic agent, 0.3kg of silane coupling agent, 76.0kg of deionized water, 1kg of composite photocatalyst, and stir evenly. It is added to the oiler for drawing fiber filaments, and then the fiber filaments are dried, twisted, twisted, and woven in the same process to make filter cloth, and filled into the reaction vessel for experimental testing. Use gas chromatography to test the integrated area of the chromatographic peak of formaldehyde in the sample to reflect the change in the amount and concentration of formaldehyde.
[0048] According to the process method described in this embodiment, from configuring the sizing agent, drawing the fiber filament to obtaining the final product, the entire process time is also about 5 hours, and the transfer process usually takes 20 hours. It can be seen that after the composite photocatalyst is integrated with the common fiber ...
PUM
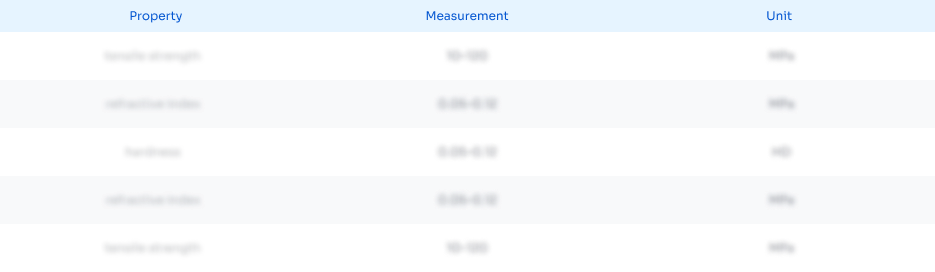
Abstract
Description
Claims
Application Information

- R&D
- Intellectual Property
- Life Sciences
- Materials
- Tech Scout
- Unparalleled Data Quality
- Higher Quality Content
- 60% Fewer Hallucinations
Browse by: Latest US Patents, China's latest patents, Technical Efficacy Thesaurus, Application Domain, Technology Topic, Popular Technical Reports.
© 2025 PatSnap. All rights reserved.Legal|Privacy policy|Modern Slavery Act Transparency Statement|Sitemap|About US| Contact US: help@patsnap.com