Anticorrosive material for metallic equipment and preparation and construction methods thereof
A technology of anti-corrosion materials and anti-corrosion coatings, applied in the field of materials, can solve the problems of reduced salt spray resistance, coating adhesion, mechanical properties of impact resistance, equipment damage, etc., to achieve accelerated speed, small construction environment, and guaranteed construction. effect of progress
- Summary
- Abstract
- Description
- Claims
- Application Information
AI Technical Summary
Problems solved by technology
Method used
Image
Examples
preparation example Construction
[0048] refer to figure 1 , which shows a flow chart of a method for preparing the rubber asphalt anticorrosion coating in an anticorrosion material for metal equipment according to an embodiment of the present invention, and the preparation method specifically includes:
[0049] Step 101. Preparation of vulcanized rubber-modified anionic emulsified asphalt: mixing asphalt and vulcanized rubber and emulsifying to prepare vulcanized rubber-modified anionic emulsified asphalt.
[0050] Step 102. Preparation of the antirust agent: adding one or more of zinc phosphate, modified zinc phosphate, and zinc molybdate, and wetting agent, deionized water, and surfactant in proportion to prepare an antiseptic Crude product, the crude product of the anti-rust agent is dispersed at a speed of 1000-2000r / min, the dispersion time is 1h, and then the crude product of the dispersed anti-rust agent is ground, and the grinding time is 1h to obtain the anti-rust agent .
[0051] Step 103, prepara...
Embodiment 1
[0060] When preparing rubber asphalt anticorrosion coatings for metal equipment anticorrosion materials, 63kg of asphalt and 27kg of vulcanized rubber were mixed and then emulsified to obtain 90kg of vulcanized rubber modified anionic emulsified asphalt.
[0061] Add successively 0.1kg of rosin soap and fatty acid soap, 0.1kg of wetting agent, 0.1kg of polynaphthalene sulfonic acid sodium salt, 0.1kg of deionized water and 0.1kg of zinc phosphate to mix to obtain the rust inhibitor crude product, and the The rust preventive crude product is dispersed at a speed of 1000r / min for 1 hour, and then the dispersed rust preventive crude product is ground for 1 hour to obtain a total amount of 0.5 kg of the rust preventive. .
[0062] Put 0.1kg of rosin soap and fatty acid soap, 0.1kg of dispersant, 0.1kg of sodium alkyl sulfate, 0.1kg of hindered amine light stabilizer, 0.1kg of defoamer and 0.1kg of anti-aging agent at 500r / min Mix and disperse at a rotating speed for 1 hour to pre...
Embodiment 2
[0065] When preparing rubber asphalt anticorrosion coatings for metal equipment anticorrosion materials, 63kg of asphalt and 27kg of vulcanized rubber were mixed and then emulsified to obtain 90kg of vulcanized rubber modified anionic emulsified asphalt.
[0066] Add 0.1kg of rosin soap and fatty acid soap, 0.1kg of wetting agent, 0.1kg of sodium polynaphthalene sulfonate, 0.1kg of deionized water, 0.1kg of zinc phosphate, 0.1kg of modified zinc phosphate and 0.1 kg of zinc molybdate mixed to obtain the rust preventive crude product mixed to obtain the rust preventive crude product, the rust preventive crude product was dispersed at a speed of 1000r / min for a dispersion time of 1h, and then the dispersed rust preventive The crude product of the agent was ground for 1 hour to obtain a total amount of 0.7 kg of the antirust agent.
[0067] Put 0.1kg of rosin soap and fatty acid soap, 0.1kg of dispersant, 0.1kg of sodium alkyl sulfate, 0.1kg of hindered amine light stabilizer, 0....
PUM
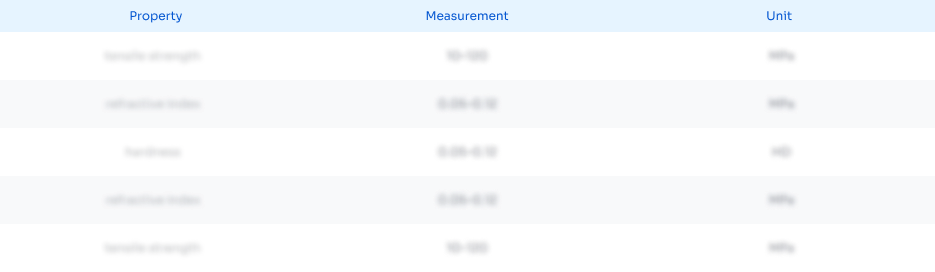
Abstract
Description
Claims
Application Information

- Generate Ideas
- Intellectual Property
- Life Sciences
- Materials
- Tech Scout
- Unparalleled Data Quality
- Higher Quality Content
- 60% Fewer Hallucinations
Browse by: Latest US Patents, China's latest patents, Technical Efficacy Thesaurus, Application Domain, Technology Topic, Popular Technical Reports.
© 2025 PatSnap. All rights reserved.Legal|Privacy policy|Modern Slavery Act Transparency Statement|Sitemap|About US| Contact US: help@patsnap.com