Synthesis process of viscosified phenyl silicone oil for high-power light-emitting diode (LED) packaging
A technology of LED encapsulation and phenyl silicone oil, which is applied in electrical components, circuits, semiconductor devices, etc., can solve the problems of relying on imports of silica gel for high-power LED encapsulation, not being able to meet the needs of power LED encapsulation, and being expensive, and achieve good room temperature Curing performance, improvement of light output and high temperature resistance, and effect of improving adhesion
- Summary
- Abstract
- Description
- Claims
- Application Information
AI Technical Summary
Problems solved by technology
Method used
Image
Examples
Embodiment 1
[0029] A. Synthesis of epoxy end-capping agent: take a four-necked flask, set a condenser, a nitrogen conduit, and a built-in thermometer; put allyl glycidyl ether and platinum catalyst into the four-necked flask according to the molar ratio of 1:0.001:0.45 , put 1,1,3,3-tetramethyldisiloxane in the dropping funnel, and add allyl glycidyl ether, platinum catalyst and 1,1,3,3-tetramethyldisiloxane into the four-necked flask Toluene, which is twice the total mass of methyldisiloxane, is used as a solvent; 1,1,3,3-Tetramethyldisiloxane is dropped at a rate of 5 drops per minute at a temperature of 65°C under nitrogen protection. Add it into a four-neck flask, after the dropwise addition, raise the temperature to 95°C for 10 hours, then heat up and distill, the component distilled at 195°C is the epoxy end-capping agent 1,1,3,3-tetramethyl- 1,3 Bis[3-(oxiranylmethoxy)propyl]disiloxane; 95% yield.
[0030] B. Dewatering of raw materials: According to the application field of pheny...
Embodiment 2
[0035] A. Synthesis of epoxy end-capping agent: Take a four-necked flask, set a condenser, a nitrogen conduit, and a built-in thermometer; put allyl glycidyl ether and platinum catalyst into the four-necked flask according to the molar ratio of 1:0.01:0.5 , put 1,1,3,3-tetramethyldisiloxane in the dropping funnel, and add allyl glycidyl ether, platinum catalyst and 1,1,3,3-tetramethyldisiloxane into the four-necked flask Toluene twice the total mass of methyldisiloxane is used as solvent; 1,1,3,3-Tetramethyldisiloxane is dropped at a rate of 7 drops per minute at a temperature of 60°C under nitrogen protection conditions Add it into a four-necked flask, after the dropwise addition, raise the temperature to 100°C to react for 8 hours, then heat up and distill, the component distilled at 200°C is the epoxy end-capping agent 1,1,3,3-tetramethyl- 1,3 Bis[3-(oxiranylmethoxy)propyl]disiloxane; 75% yield.
[0036] B. Dewatering of raw materials: According to the application field of...
Embodiment 3
[0041] A. Synthesis of epoxy end-capping agent: take a four-necked flask, set a condenser, a nitrogen conduit, and a built-in thermometer; put allyl glycidyl ether and platinum catalyst into the four-necked flask according to the molar ratio of 1:0.005:0.40 , put 1,1,3,3-tetramethyldisiloxane in the dropping funnel, and add allyl glycidyl ether, platinum catalyst and 1,1,3,3-tetramethyldisiloxane into the four-necked flask Toluene, which is twice the total mass of methyldisiloxane, is used as a solvent; 1,1,3,3-Tetramethyldisiloxane is dropped at a rate of 5 drops per minute at a temperature of 70°C under nitrogen protection. Add it into a four-neck flask, after the dropwise addition, raise the temperature to 97°C for 10 hours, then heat up and distill, the component distilled at 180°C is the epoxy-capping agent 1,1,3,3- 1,3 Bis[3-(oxiranylmethoxy)propyl]disiloxane; 88% yield.
[0042] B. Dewatering of raw materials: According to the application field of phenyl silicone oil, ...
PUM
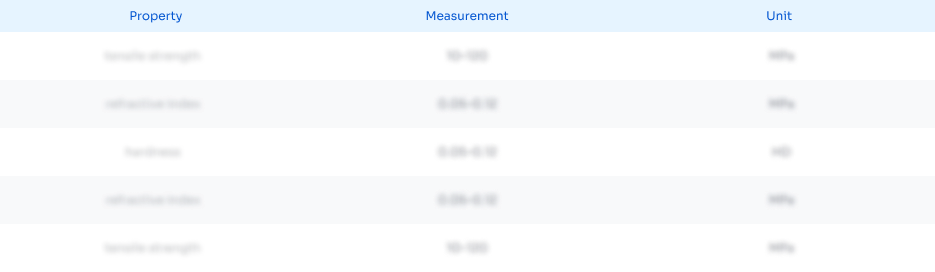
Abstract
Description
Claims
Application Information

- R&D Engineer
- R&D Manager
- IP Professional
- Industry Leading Data Capabilities
- Powerful AI technology
- Patent DNA Extraction
Browse by: Latest US Patents, China's latest patents, Technical Efficacy Thesaurus, Application Domain, Technology Topic, Popular Technical Reports.
© 2024 PatSnap. All rights reserved.Legal|Privacy policy|Modern Slavery Act Transparency Statement|Sitemap|About US| Contact US: help@patsnap.com