Process for producing biurea through optimized urea method
A technology of biurea and urea, applied in the field of biurea, can solve the problems of increasing the consumption of caustic soda, and achieve the effects of low cost, low consumption of raw materials and energy, and high yield in a single kettle
- Summary
- Abstract
- Description
- Claims
- Application Information
AI Technical Summary
Problems solved by technology
Method used
Examples
Embodiment 1
[0029] (1) Mix sodium hypochlorite and urea solution (catalyst has been added) and send it into the hydrazine hydrate reactor, heat it to 125°C with steam, and obtain a crude solution containing about 46g / L hydrazine hydrate after the reaction, and send this solution directly to Into the evaporator, evaporate and concentrate under vacuum conditions to a crude solution containing 85g / L hydrazine hydrate, the concentration ratio is 1:0.58, and the concentrated and separated sodium chloride is sent to a centrifuge to separate the sodium chloride. The evaporated steam containing a small amount of hydrazine hydrate enters the rectification tower and is concentrated to 10-15% hydrazine hydrate.
[0030] (2) The crude solution obtained from (1) is extracted from the evaporator, sent to the pre-cooling tank and cooled to 35-45°C with circulating water under stirring, and then sent to the crystallization kettle to be cooled to 0°C with frozen brine , separate out the sodium carbonate d...
Embodiment 2
[0037] (1) The crude solution containing 46g / L hydrazine hydrate that is 125°C from the hydrazine hydrate reactor is sent into the crystallization kettle after pre-cooling and cooled to 0°C with frozen brine, and the separated out Sodium carbonate decahydrate is sent to Centrifuge separates sodium carbonate decahydrate crystal, obtains the essence hydrazine liquid containing 53g / L hydrazine hydrate.
[0038] (2) The hydrazine solution obtained in (1) is preheated and sent to the evaporator, and evaporated and concentrated to a crude solution containing 85g / L hydrazine hydrate under vacuum conditions, the concentration ratio is 1:0.65, and the separated out Sodium chloride is sent to centrifuge to separate solid sodium chloride. The evaporated steam containing a small amount of hydrazine hydrate enters the rectification tower and is concentrated to 10-15% hydrazine hydrate.
[0039] (3) After the crude solution obtained from (2) is pre-cooled to 35-45°C, it is sent to the crys...
PUM
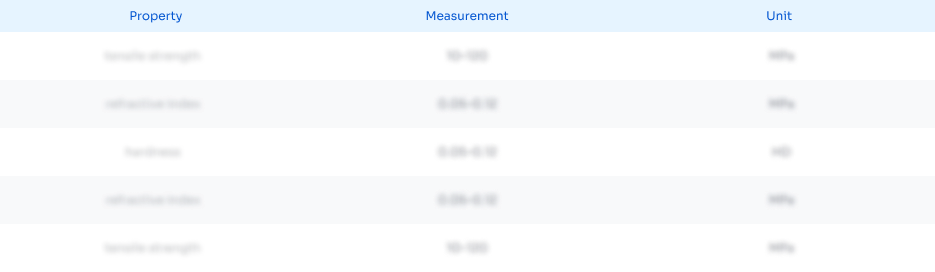
Abstract
Description
Claims
Application Information

- R&D
- Intellectual Property
- Life Sciences
- Materials
- Tech Scout
- Unparalleled Data Quality
- Higher Quality Content
- 60% Fewer Hallucinations
Browse by: Latest US Patents, China's latest patents, Technical Efficacy Thesaurus, Application Domain, Technology Topic, Popular Technical Reports.
© 2025 PatSnap. All rights reserved.Legal|Privacy policy|Modern Slavery Act Transparency Statement|Sitemap|About US| Contact US: help@patsnap.com