Method for treating ash deposition and scaling of GGH (gas-gas heater)
A flue gas heat exchanger and ash accumulation technology, which is applied in the direction of cleaning heat transfer devices, lighting and heating equipment, flushing, etc., can solve problems such as channel narrowing, poor demister effect, nozzle clogging, etc., and reduce downtime The number of times, the effect of ensuring normal operation and ensuring safe operation
- Summary
- Abstract
- Description
- Claims
- Application Information
AI Technical Summary
Problems solved by technology
Method used
Examples
Embodiment 1
[0018] A method for dealing with fouling of flue gas heat exchanger GGH, comprising the following steps:
[0019] (1) On-line compressed air soot blowing: Use 0.6MPa compressed air to carry out on-line purge and dust accumulation on the GGH, and the cleaning frequency is once every 2 hours;
[0020] (2) On-line high-pressure water flushing: Use 10MPa domestic fire-fighting water for online high-pressure water flushing for long-term accumulated adherents that cannot be removed by normal dry methods;
[0021] (3) Low-pressure water flushing before shutdown: Before GGH shutdown, use 0.4MPa desulfurization process water for low-pressure flushing to remove loose acidic deposits adhering to the GGH rotor;
[0022] (4) High-pressure flushing with chemical cleaning agent after shutdown: soak the GGH heat exchange plate with CHT-2013 GGH alkaline cleaning agent and then flush it with 40MPa high-pressure water.
Embodiment 2
[0024] A method for dealing with fouling of flue gas heat exchanger GGH, comprising the following steps:
[0025] (1) On-line compressed air soot blowing: use 0.9MPa compressed air to carry out on-line purge and dust accumulation on the GGH, and the cleaning frequency is once every 3 hours;
[0026] (2) On-line high-pressure water flushing: Use 13MPa domestic fire-fighting water for online high-pressure water flushing for long-term accumulated adherents that cannot be removed by normal dry methods;
[0027] (3) Low-pressure water flushing before shutdown: Before GGH shutdown, use 0.55MPa desulfurization process water for low-pressure flushing to remove loose acidic deposits adhering to the GGH rotor;
[0028] (4) High-pressure flushing with chemical cleaning agent after shutdown: soak the GGH heat exchange plate with GS-QS01 GGH enamel original cleaner and GS-QS02 GGH enamel original cleaner and rinse with 40MPa high-pressure water.
[0029] The above are the preferred embodi...
PUM
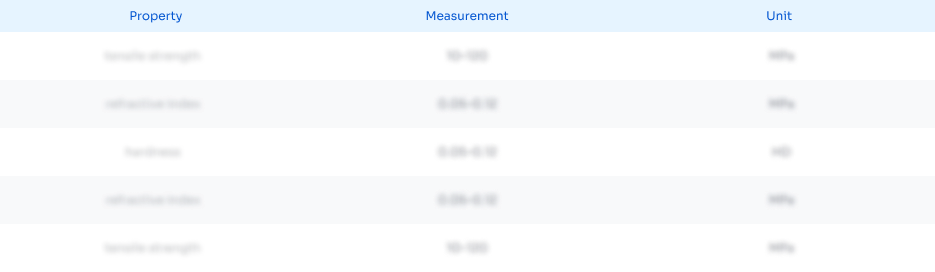
Abstract
Description
Claims
Application Information

- R&D Engineer
- R&D Manager
- IP Professional
- Industry Leading Data Capabilities
- Powerful AI technology
- Patent DNA Extraction
Browse by: Latest US Patents, China's latest patents, Technical Efficacy Thesaurus, Application Domain, Technology Topic, Popular Technical Reports.
© 2024 PatSnap. All rights reserved.Legal|Privacy policy|Modern Slavery Act Transparency Statement|Sitemap|About US| Contact US: help@patsnap.com