Method for improving electroplating layer uniformity of PCB (printed circuit board) vertical electroplating line
A vertical electroplating and electroplating layer technology, applied in the direction of electrodes, electrolytic process, electrolytic components, etc., to achieve the effects of uniform power lines, reduced copper consumption, and uniform current distribution
- Summary
- Abstract
- Description
- Claims
- Application Information
AI Technical Summary
Problems solved by technology
Method used
Image
Examples
Embodiment 1
[0027] combined with figure 1 As shown, the present embodiment discloses a method for improving the uniformity of the electroplating layer of PCB vertical electroplating lines, including the following steps:
[0028] S1: The lower ends of the two anodes 2 in the electroplating copper cylinder 1 are respectively connected to the corresponding conductive rods 3;
[0029] S2: Connect the two conductive rods to the anode 2 of the rectifier;
[0030] S3: connecting the flying target 4 in the electroplating copper cylinder to the cathode of the rectifier;
[0031] S4: hang the PCB production board 5 on the flying target;
[0032] S5: setting the anode 2 current introduction point at the lower end of the conductive rod;
[0033] S6: energize the cathode and anode, and perform electroplating treatment on the PCB production board 5 to be electroplated.
[0034] Wherein, the upper end of the PCB production board 5 is clamped on the flying target; and the electroplating current is se...
PUM
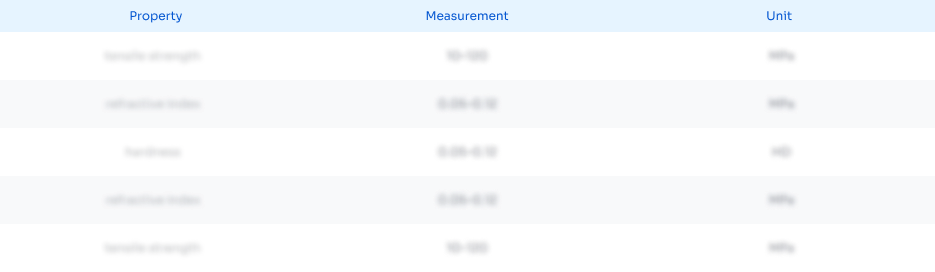
Abstract
Description
Claims
Application Information

- R&D Engineer
- R&D Manager
- IP Professional
- Industry Leading Data Capabilities
- Powerful AI technology
- Patent DNA Extraction
Browse by: Latest US Patents, China's latest patents, Technical Efficacy Thesaurus, Application Domain, Technology Topic, Popular Technical Reports.
© 2024 PatSnap. All rights reserved.Legal|Privacy policy|Modern Slavery Act Transparency Statement|Sitemap|About US| Contact US: help@patsnap.com