Hot-rolling production method for low-nickel austenitic stainless steel coils
A technology of austenitic stainless steel and production method, applied in the field of low-nickel austenitic stainless steel coil products, can solve the problems of narrow hot working range, surface cracks and edge cracks, large deformation rate, etc., and achieve the effect of reasonable formula
- Summary
- Abstract
- Description
- Claims
- Application Information
AI Technical Summary
Problems solved by technology
Method used
Image
Examples
Embodiment 1
[0029] The low-nickel austenitic stainless steel used in this example is composed by mass: C: ≤0.15%; Mn: 8-11%; P: ≤0.045%; S: ≤0.03%; Si: ≤1.0%; Cr: 13 ~17%; Ni: 1.0~2.0%; Mo: ≤0.8%; N: 0.1~0.20%; Cu: 0.5~1.5%; the balance is Fe.
[0030] The rolling process of the low-nickel austenitic stainless steel coil with a thickness of 4.6mm is: grinding→heating→phosphorus removal by high-pressure water→rough rolling→finish rolling→laminar cooling→coiling.
[0031] (1) Grind the 200mm thick continuous casting slab through 26 and 32 mesh grinding wheels respectively;
[0032] (2) After the continuous casting slab is ground, it goes through the preheating section, the first stage of heating, the second stage of heating and the soaking section before being released from the furnace. The temperature of the soaking section is 1240 ° C, the holding time of the soaking section is 60 minutes, and the total time in the furnace is 200 ~240min, the temperature of the upper surface of the conti...
Embodiment 2
[0038] The low-nickel austenitic stainless steel used in this example is composed by mass: C: ≤0.15%; Mn: 8-11%; P: ≤0.045%; S: ≤0.03%; Si: ≤1.0%; Cr: 13 ~17%; Ni: 1.0~2.0%; Mo: ≤0.8%; N: 0.1~0.20%; Cu: 0.5~1.5%; the balance is Fe.
[0039] The rolling process of the low-nickel austenitic stainless steel coil with a thickness of 9.0mm is: grinding→heating→phosphorus removal by high-pressure water→rough rolling→finish rolling→laminar cooling→coiling.
[0040] (1) Grind the 200mm thick continuous casting slab through 26 and 32 mesh grinding wheels respectively;
[0041] (2) After the continuous casting slab is ground, it goes through the preheating section, the first stage of heating, the second stage of heating and the soaking section, and then comes out of the furnace. ~240min, the temperature of the upper surface of the continuous casting slab is 15°C lower than that of the lower surface before being released from the furnace;
[0042] (3) During high-pressure water dephospho...
Embodiment 3
[0047] The low-nickel austenitic stainless steel used in this example is composed by mass: C: ≤0.15%; Mn: 8-11%; P: ≤0.045%; S: ≤0.03%; Si: ≤1.0%; Cr: 13 ~17%; Ni: 1.0~2.0%; Mo: ≤0.8%; N: 0.1~0.20%; Cu: 0.5~1.5%; the balance is Fe.
[0048] The rolling process of the low-nickel austenitic stainless steel coil with a thickness of 2.5mm is: grinding→heating→phosphorus removal by high-pressure water→rough rolling→finish rolling→laminar cooling→coiling.
[0049] (1) Grind the 200mm thick continuous casting slab through 26 and 32 mesh grinding wheels respectively;
[0050] (2) After the continuous casting slab is ground, it goes through the preheating section, the first stage of heating, the second stage of heating and the soaking section, and then comes out of the furnace. ~240min, the temperature of the upper surface of the continuous casting slab is 15°C lower than that of the lower surface before being released from the furnace;
[0051] (3) During high-pressure water dephosp...
PUM
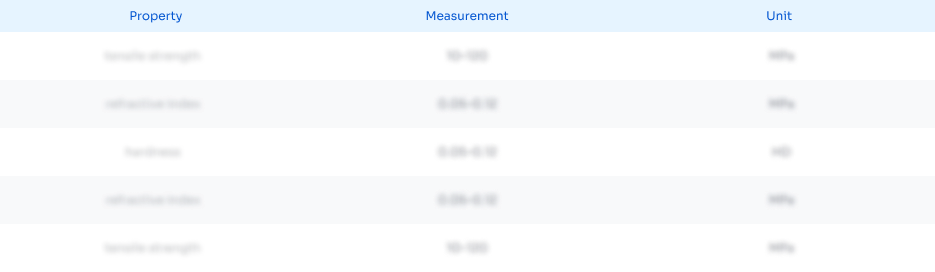
Abstract
Description
Claims
Application Information

- R&D
- Intellectual Property
- Life Sciences
- Materials
- Tech Scout
- Unparalleled Data Quality
- Higher Quality Content
- 60% Fewer Hallucinations
Browse by: Latest US Patents, China's latest patents, Technical Efficacy Thesaurus, Application Domain, Technology Topic, Popular Technical Reports.
© 2025 PatSnap. All rights reserved.Legal|Privacy policy|Modern Slavery Act Transparency Statement|Sitemap|About US| Contact US: help@patsnap.com