Method for rapidly manufacturing recombinant bamboo
A recombined bamboo and fast technology, which is applied in the field of fire doors, can solve the problems of manual mold loading and unloading, high labor intensity of workers, and small scope of application, so as to achieve the effect of ensuring smoothness, low labor intensity of workers, and reducing health maintenance time
- Summary
- Abstract
- Description
- Claims
- Application Information
AI Technical Summary
Problems solved by technology
Method used
Examples
Embodiment 1
[0042] A method for rapidly manufacturing recombined bamboo, is characterized in that: comprises the following steps:
[0043] 1. Select uniform bamboo;
[0044] 2. Pave the bamboo evenly layer by layer according to the required board thickness and apply glue to form a pre-pressed bamboo board;
[0045] 3. Push the pre-pressed bamboo board into the high-frequency heat press machine;
[0046] 4. Pre-press the pre-pressed bamboo board, that is, press the upper and side pressing boards of the high-frequency hot press on the upper surface and the side of the bamboo board respectively to apply pressure;
[0047] 5. Turn on the high-frequency heat press and carry out high-frequency heat pressing for 6-45 minutes to make bamboo boards;
[0048] 6. After the high-frequency hot pressing is finished, air-supply the bamboo board and let it stand;
[0049] 7. Remove the pressure on the bamboo board after the air supply is finished, that is, remove the pressure exerted on the bamboo boa...
Embodiment 2
[0063] The difference from the above-mentioned embodiment is that the bamboo board is made by high-frequency hot pressing for 45 minutes; the pressure applied by the upper pressing plate and the side pressing plate to the pre-pressed bamboo board in the step 4 is 10 Mpa, and in the step 5, the high-frequency During the hot-pressing process, the pre-pressed bamboo board was re-pressed to 14 Mpa.
[0064] In the step five, the high frequency is switched off every 2 minutes after being switched on, and the high frequency is switched on again after a 1 minute stop, and the operation is repeated 15 times.
[0065] The time for the air supply to stand still in the step 6 is 30 minutes. The spray cooling time is 20 minutes.
Embodiment 3
[0067] The difference from the above-mentioned embodiment is that: carry out high-frequency hot pressing for 30 minutes to obtain the bamboo board; the pressure applied by the upper pressing plate and the side pressing board to the pre-pressed bamboo board in the step 4 is 9Mpa, and in the step 5, the high-frequency heating During the pressing process, the pre-pressed bamboo boards were re-pressed to 12 Mpa.
[0068] In the step five, the high frequency is switched off every 2 minutes after being switched on, and the high frequency is switched on again after a 1 minute stop, and the operation is repeated 7 times.
[0069] The time for the air supply to stand still in the step 6 is 20 minutes. The spray cooling time is 40 minutes.
PUM
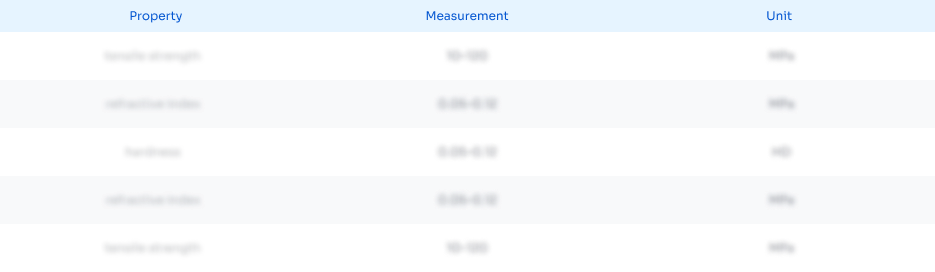
Abstract
Description
Claims
Application Information

- R&D
- Intellectual Property
- Life Sciences
- Materials
- Tech Scout
- Unparalleled Data Quality
- Higher Quality Content
- 60% Fewer Hallucinations
Browse by: Latest US Patents, China's latest patents, Technical Efficacy Thesaurus, Application Domain, Technology Topic, Popular Technical Reports.
© 2025 PatSnap. All rights reserved.Legal|Privacy policy|Modern Slavery Act Transparency Statement|Sitemap|About US| Contact US: help@patsnap.com