Method for prolonging operation cycle of deoxidized biomass oil hydrogenation device
A biomass oil and hydrogenation treatment technology, which is applied in the fields of hydrogenation treatment process, hydrocarbon oil treatment, petroleum industry, etc., can solve the problems of prolonging the operation cycle of deoxygenated biomass oil hydrogenation equipment, rapid coking, etc., and avoid the tendency of coking , Efficient use of energy, and the effect of extending the operating cycle
- Summary
- Abstract
- Description
- Claims
- Application Information
AI Technical Summary
Problems solved by technology
Method used
Examples
Embodiment 1
[0025] The method for prolonging the operating cycle of the deoxygenated biomass oil hydrogenation unit of this embodiment includes:
[0026] Step 1: deoxygenated straw pyrolysis oil (flow rate 1.25m 3 / h, pressure 11.5MPa, temperature 45°C) with the mixed hydrogen delivered by the compressor (flow 650Nm 3 / h, purity 90%, temperature 55°C, pressure 11.7MPa) mixing;
[0027] Step 2: Use the outlet heat exchanger of the main hydrogenation reactor to exchange the heat of the deoxygenated straw cracking oil and mixed hydrogen mixture to 170°C and enter the pre-hydrogenation reactor. Under the conditions of reaction temperature 180°C and reaction pressure 11MPa, the deoxygenated straw is cracked The mixture of oil and mixed hydrogen is subjected to low-temperature pre-hydrogenation reaction in the pre-hydrogenation reactor;
[0028] Step 3: The effluent from the pre-hydrogenation reactor enters the heating furnace to be heated to 340°C, and then enters the main hydrogenation reac...
Embodiment 2
[0031] The method for prolonging the operating cycle of the deoxygenated biomass oil hydrogenation unit of this embodiment includes:
[0032] Step 1: Deoxidized sawdust pyrolysis oil (flow 3.75m 3 / h, pressure 13.5MPa, temperature 50℃) with the mixed hydrogen delivered by the compressor (flow 4411Nm 3 / h, purity 85%, temperature 65°C, pressure 13.7MPa) mixing;
[0033] Step 2: Use a preheating furnace to exchange heat for the mixture of deoxidized wood cracking oil and mixed hydrogen to 180°C and enter the prehydrogenation reactor. Under the conditions of a reaction temperature of 190°C and a reaction pressure of 13 MPa, the mixture of deoxidized sawdust pyrolysis oil and hydrogen is subjected to a low-temperature pre-hydrogenation reaction in a pre-hydrogenation reactor;
[0034] Step 3: The effluent of the pre-hydrogenation reactor enters the heating furnace and is heated to 400°C before entering the main hydrogenation reactor. Under the conditions of a reaction temperatur...
Embodiment 3
[0037] The method for prolonging the operating cycle of the deoxygenated biomass oil hydrogenation unit of this embodiment includes:
[0038] Step 1: Deoxidized biomass oil is mixed with hydrogen to form a mixture of deoxygenated biomass oil and hydrogen;
[0039]Step 2: Use the waste heat of the device or a low-temperature heating furnace to exchange heat or heat the mixture of deoxidized biomass oil and hydrogen to 100°C, and then enter the pre-hydrogenation reactor for low-temperature pre-hydrogenation; the reaction pressure of low-temperature pre-hydrogenation is 10MPa , the reaction temperature is 120°C, the volume ratio of hydrogen to oil is 340, and the volume space velocity is 0.5h -1 ;
[0040] Step 3: The effluent of the pre-hydrogenation reactor is heated to 280°C in a heating furnace and enters the main hydrogenation reactor for high-temperature hydrogenation to obtain a high-temperature hydrogenation product; the reaction pressure of the high-temperature hydrogen...
PUM
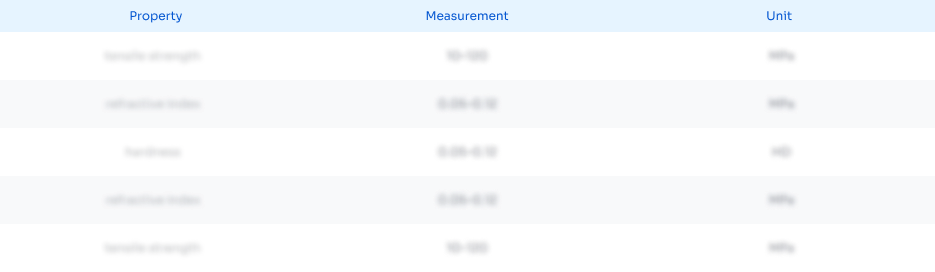
Abstract
Description
Claims
Application Information

- R&D Engineer
- R&D Manager
- IP Professional
- Industry Leading Data Capabilities
- Powerful AI technology
- Patent DNA Extraction
Browse by: Latest US Patents, China's latest patents, Technical Efficacy Thesaurus, Application Domain, Technology Topic, Popular Technical Reports.
© 2024 PatSnap. All rights reserved.Legal|Privacy policy|Modern Slavery Act Transparency Statement|Sitemap|About US| Contact US: help@patsnap.com