Paper pulp molding forming machine
A molding machine and pulp molding technology, used in textiles and papermaking, can solve the problems of high gas consumption, pollution of pulp preparation, waste of time, etc., and achieve the effects of improving accuracy and stability, solving pollution problems, and reducing production costs.
- Summary
- Abstract
- Description
- Claims
- Application Information
AI Technical Summary
Problems solved by technology
Method used
Image
Examples
Embodiment Construction
[0028] In order to make the object, technical solution and advantages of the present invention clearer, the present invention will be further described in detail below in conjunction with the accompanying drawings and embodiments. It should be understood that the specific embodiments described here are only used to explain the present invention, not to limit the present invention.
[0029] In the description of the present invention, it needs to be understood that "the first servo motor" and "the second servo motor", "the first reducer" and "the second reducer", and the "first guide ventilation rod" and "the second Guide ventilation rod", and "first ball screw" and "second ball screw" are for the convenience of describing the present invention and simplifying the description, rather than referring to the specific motor, reducer, guide ventilation rod that the pulp molding machine has. rod and ball screw. In addition, the idioms "first" and "second" are used for descriptive pu...
PUM
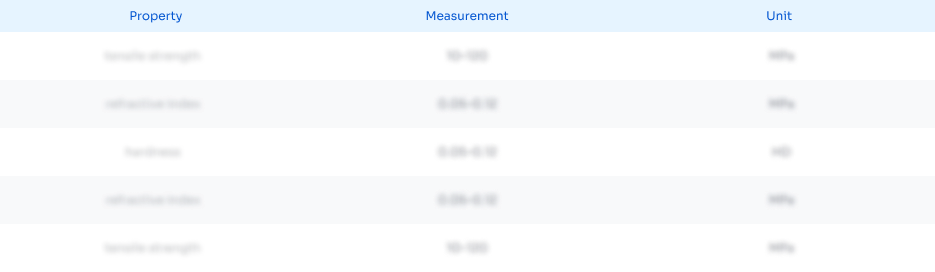
Abstract
Description
Claims
Application Information

- R&D
- Intellectual Property
- Life Sciences
- Materials
- Tech Scout
- Unparalleled Data Quality
- Higher Quality Content
- 60% Fewer Hallucinations
Browse by: Latest US Patents, China's latest patents, Technical Efficacy Thesaurus, Application Domain, Technology Topic, Popular Technical Reports.
© 2025 PatSnap. All rights reserved.Legal|Privacy policy|Modern Slavery Act Transparency Statement|Sitemap|About US| Contact US: help@patsnap.com