Water treatment filter material filter membrane alloy disc stripping machine and using method thereof
A water treatment and peeling machine technology, applied in separation methods, filtration separation, chemical instruments and methods, etc., can solve the loss of filtration effect of filter materials, iron and manganese cannot be effectively removed, increase backwash time, water consumption and electricity consumption and other problems, to achieve the effect of low operating costs
- Summary
- Abstract
- Description
- Claims
- Application Information
AI Technical Summary
Problems solved by technology
Method used
Image
Examples
Embodiment Construction
[0026] The present invention will be further described below in conjunction with the accompanying drawings.
[0027] Depend on figure 1 A water treatment filter material filter membrane alloy disc stripping machine is shown, including a motor stripping system 1, a high-pressure water system 2, a filter sand circulation system 3, a translational lifting system 4, a cantilever rod assembly 5, a door hanger 6, Main frame 7, distribution box 8.
[0028] Depend on figure 2 The motor peeling system shown, the motor peeling system 1 includes a washing machine 21, a frequency conversion speed regulation motor A22, a sand suction pump 23, a frequency conversion speed regulation motor B24, wherein a pair of alloys arranged oppositely are arranged in the washing machine 21 Grinding disc, replaceable, the diameter of the alloy grinding disc is 330mm, and the distance between the two alloy grinding discs is adjustable to 10mm. The two alloy grinding discs are evenly arranged with ribs f...
PUM
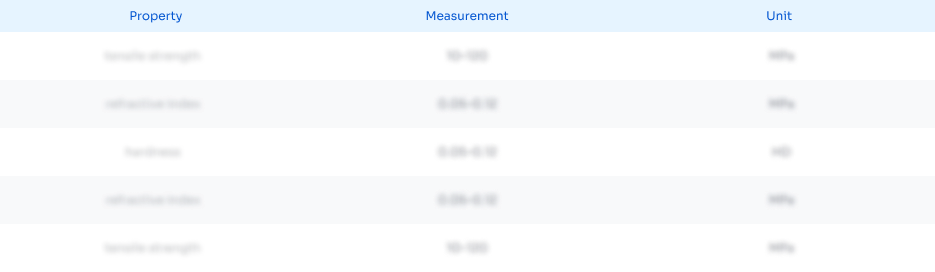
Abstract
Description
Claims
Application Information

- R&D Engineer
- R&D Manager
- IP Professional
- Industry Leading Data Capabilities
- Powerful AI technology
- Patent DNA Extraction
Browse by: Latest US Patents, China's latest patents, Technical Efficacy Thesaurus, Application Domain, Technology Topic, Popular Technical Reports.
© 2024 PatSnap. All rights reserved.Legal|Privacy policy|Modern Slavery Act Transparency Statement|Sitemap|About US| Contact US: help@patsnap.com