Method for producing high-purity zirconium oxychloride and co-producing silicon tetrachloride through zircon sand boiling chlorination method
A technology of boiling chlorination and pure zirconium oxychloride, which is applied in the direction of zirconium halide, silicon halide compound, halosilane, etc., can solve the problem of high production cost, increased production cost, and product quality that cannot reach high-purity zirconium oxychloride Quality standards and other issues to achieve the effect of low production cost and good product quality
- Summary
- Abstract
- Description
- Claims
- Application Information
AI Technical Summary
Problems solved by technology
Method used
Image
Examples
Embodiment 1
[0041] Process route see figure 1 , specifically prepared as:
[0042] 1) Chlorination reaction
[0043] The raw material zircon sand, calcined petroleum coke and silicon carbide are added to the mixer according to the mass ratio of zircon sand: calcined coke: silicon carbide = 1:0.22:0.34, and the materials are mixed, and then added to the front of the furnace The silo is continuously fed into the chlorination furnace through a screw conveyor.
[0044]Chlorine gas is fed into the bottom of the chlorination furnace, and the weight of the feed is zircon sand: chlorine gas = 1: 2.78. The chlorine gas enters the reaction section through the distributor to react with the raw materials. The reaction temperature is controlled at 1170 °C, and the furnace pressure is controlled within 3000 Pa. At the same time Determine the slag removal time of the chlorination furnace according to the furnace pressure, and control the chlorine flow rate at 0.009m / s, so that the reaction can proceed...
Embodiment 2
[0081] In Example 1, the silicon tetrachloride-containing tail gas obtained by the cooling treatment of the quencher enters the gas-solid separation of the gas, and the solid obtained is a zirconium tetrachloride solid, which enters the purifier for purification, then enters the hydrolysis tank through a screw conveyor, and adds Pure water, evaporating acid, and washing liquid are used for hydrolysis, and the amount of material added is zirconium tetrachloride
[0082] Solid: pure water: evaporating acid: washing liquid is 0.91:2.35:0.72:1.00 (weight ratio), control the hydrolysis temperature at 40-50°C, the speed of the mixer in the hydrolysis tank is 100r / min, and the concentration of zirconium in the hydrolysis solution is 100±10g / l, use a pump to send it into a chamber filter press to filter out the entrained solids to obtain a purified zirconium oxychloride solution, and the washing solution during hydrolysis can be recycled and reused. Wherein, the evaporating acid is 2...
Embodiment 3
[0095] The primary mother liquor prepared in the above-mentioned embodiment 1 or embodiment 2 is subjected to pressurized evaporation, and the primary crystallization mother liquor enters a double-heating external circulation graphite evaporator, uses steam to heat the mother liquor, and uses the secondary steam of the evaporator as a heat source to preheat the mother liquor solution , control the vapor pressure at 0.3MPa-0.7MPa, and the secondary pressure at 0.2MPa-0.3MPa, so that the concentration of hydrochloric acid in the evaporating liquid is 17-19%, and the concentration of zirconia is 190±10g / l. Crystallization tank, crystallization at 25°C for 20h, the crystallized oxychlorination solution is filtered through a belt filter, and the filtered crystals are washed with 18% hydrochloric acid to obtain zirconium oxychloride, and the obtained filtrate is the secondary mother liquor.
[0096] The obtained zirconium oxychloride crystals are re-dissolved as crystal seeds, and t...
PUM
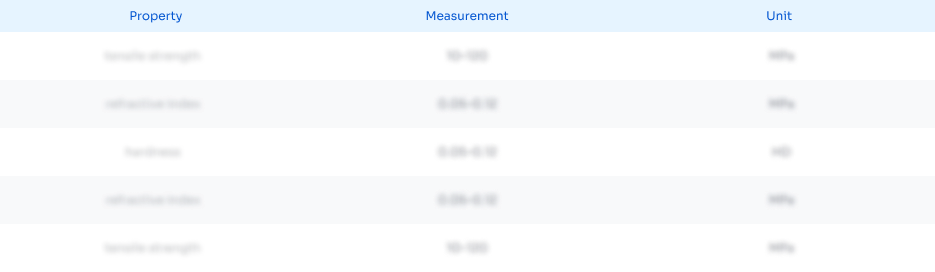
Abstract
Description
Claims
Application Information

- R&D
- Intellectual Property
- Life Sciences
- Materials
- Tech Scout
- Unparalleled Data Quality
- Higher Quality Content
- 60% Fewer Hallucinations
Browse by: Latest US Patents, China's latest patents, Technical Efficacy Thesaurus, Application Domain, Technology Topic, Popular Technical Reports.
© 2025 PatSnap. All rights reserved.Legal|Privacy policy|Modern Slavery Act Transparency Statement|Sitemap|About US| Contact US: help@patsnap.com