Continuous color knitted jean fabric pad dyeing process
A technology for knitting denim and craftsmanship, which is applied in the direction of fabric surface trimming, textile material processing, continuous processing of textile materials, etc. Effect
- Summary
- Abstract
- Description
- Claims
- Application Information
AI Technical Summary
Problems solved by technology
Method used
Examples
Embodiment 1
[0023] The singeing process uses clean energy natural gas to perform open-width open flame singeing to remove hairiness on the surface of the cloth;
[0024] The scouring and bleaching process adopts a continuous open-width scouring and bleaching method, which adopts immersion under the drum liquid and spraying with a water knife on the liquid to perform countercurrent rinsing.
[0025] The specific process is:
[0026] 1. Knitted cloth weight: 500 kg, cloth length about 1000 meters;
[0027] 2. Singeing: (vehicle speed: 50 meters per minute) total time: 20 minutes;
[0028] 3. Cooking and bleaching: (Liquid retention rate: 80%, speed: 25 meters per minute, 40 minutes in the steamer)
[0029] Total time spent: 40 minutes
[0030] Recipe: Total consumption:
[0031] Scouring agent 5 g / l 2 kg
[0032] Hydrogen peroxide stabilizer 3 g / l 1.2 kg
[0033] Chelating dispersant 3 g / l 1.2 kg
[0034] Hydrogen peroxide 30g / L 12kg
[0035] Caustic soda 8 g / l 3.2 kg
[0036] Reve...
PUM
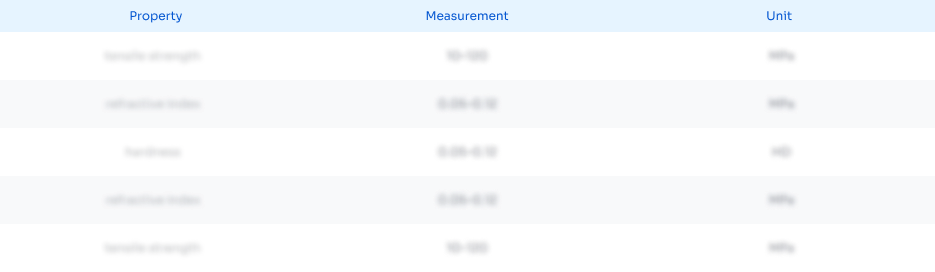
Abstract
Description
Claims
Application Information

- R&D Engineer
- R&D Manager
- IP Professional
- Industry Leading Data Capabilities
- Powerful AI technology
- Patent DNA Extraction
Browse by: Latest US Patents, China's latest patents, Technical Efficacy Thesaurus, Application Domain, Technology Topic, Popular Technical Reports.
© 2024 PatSnap. All rights reserved.Legal|Privacy policy|Modern Slavery Act Transparency Statement|Sitemap|About US| Contact US: help@patsnap.com