Rosin-based anionic coal water slurry dispersing agent and preparation method thereof
An anionic, coal-water slurry technology, applied in the field of coal-water slurry dispersant, can solve the problems of high pulp viscosity, difficult handling and high price, and achieve the effects of good dispersibility and stability and large adsorption capacity
- Summary
- Abstract
- Description
- Claims
- Application Information
AI Technical Summary
Problems solved by technology
Method used
Image
Examples
Embodiment 1
[0024] 1) Dissolve 7.1 g of dehydroabietylamine in 50.0 g of chloroform to make a solution. Add 4.6g of cyanuric chloride and 40.0g of chloroform into the reaction flask, and stir for 10min under ice-water bath. Add the above-mentioned dehydroabietylamine solution dropwise with a dropping funnel, and finish adding within 30 minutes. Then use 10% sodium hydroxide solution to keep the pH value of the system at 5, keep the reaction in an ice-water bath until the pH value remains unchanged, and obtain the intermediate product I.
[0025] 2) Add 10.0 g polyethylene glycol-400 and 40.0 g chloroform into another reaction flask, stir to dissolve. The temperature was raised to 35°C, and all the intermediate product I was slowly added dropwise to the reaction flask, and the dropwise addition was completed within 4 hours. Then use 10% sodium hydroxide solution to keep the pH value of the system at 6, keep the reaction until the pH value remains unchanged, and obtain the intermediate pr...
Embodiment 2
[0033] 1) Dissolve 7.1 g of dehydroabietylamine in 50.0 g of chloroform to make a solution. Add 4.6g of cyanuric chloride and 40.0g of chloroform into the reaction flask, and stir for 10min under ice-water bath. Add the above-mentioned dehydroabietylamine solution dropwise with a dropping funnel, and finish adding within 30 minutes. Then, the pH value of the system was maintained at 6 with a potassium hydroxide solution having a mass concentration of 10%, and the reaction was carried out in an ice-water bath until the pH value remained unchanged to obtain an intermediate product I.
[0034] 2) Add 15.0g polyethylene glycol-600 and 40.0g chloroform into another reaction flask, stir to dissolve. The temperature was raised to 40°C, and all the intermediate product I was slowly added dropwise to the reaction flask, and the dropwise addition was completed within 4 hours. Then use potassium hydroxide solution with a mass concentration of 10% to keep the pH value of the system at 6...
Embodiment 3
[0042] 1) Dissolve 7.1 g of dehydroabietylamine in 50.0 g of chloroform to make a solution. Add 4.6g of cyanuric chloride and 40.0g of chloroform into the reaction flask, and stir for 10min under ice-water bath. Add the above-mentioned dehydroabietylamine solution dropwise with a dropping funnel, and finish adding within 30 minutes. Then use 10% sodium hydroxide solution to keep the pH value of the system at 5, keep the reaction in an ice-water bath until the pH value remains unchanged, and obtain the intermediate product I.
[0043] 2) Add 29.9g polyethylene glycol-1200 and 40.0g chloroform into another reaction flask, stir to dissolve. The temperature was raised to 40°C, and all the intermediate product I was slowly added dropwise to the reaction flask, and the dropwise addition was completed within 4 hours. Then use 10% sodium hydroxide solution to keep the pH value of the system at 7, keep the reaction until the pH value remains unchanged, and obtain the intermediate pro...
PUM
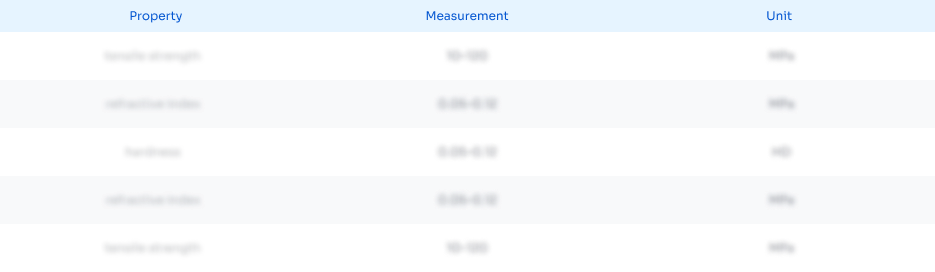
Abstract
Description
Claims
Application Information

- Generate Ideas
- Intellectual Property
- Life Sciences
- Materials
- Tech Scout
- Unparalleled Data Quality
- Higher Quality Content
- 60% Fewer Hallucinations
Browse by: Latest US Patents, China's latest patents, Technical Efficacy Thesaurus, Application Domain, Technology Topic, Popular Technical Reports.
© 2025 PatSnap. All rights reserved.Legal|Privacy policy|Modern Slavery Act Transparency Statement|Sitemap|About US| Contact US: help@patsnap.com