A resin-based composite material dust removal bag cage
A composite material and dust bag technology, which is used in the separation of dispersed particles, chemical instruments and methods, and dispersed particle filtration, etc., can solve the problems of increased cost, shortened life of steel bag cages, corrosion of dust removal skeleton, etc., and can save assembly costs. Effect
- Summary
- Abstract
- Description
- Claims
- Application Information
AI Technical Summary
Problems solved by technology
Method used
Image
Examples
Embodiment 1
[0046]Typical embodiment one: (long-term use temperature below 260°C)
[0047] Material composition (by weight ratio):
[0048] Silicone resin
35
65
[0049] Preparation:
[0050] 1. Using the winding molding process, the glass fiber soaked in resin is wound on the mold according to certain process parameters to form a net
[0051] bag cage structure.
[0052] 2. Put it in an oven at 200℃~230℃ for 4-6 hours. Put the wrapped mold into an oven for thermal curing or normal temperature curing.
[0053] 3. After curing, remove the mold and trim the corners of the cage.
Embodiment 2
[0054] Typical embodiment two: (The long-term use temperature is below 220°C)
[0055] Material composition (by weight ratio):
[0056] Novolac Epoxy Vinyl Resin
30
65
flame retardant
3
filler
2
[0057] Preparation:
[0058] 1. Stir the resin, flame retardant, filler and curing agent evenly first.
[0059] 2. After molding, heat to 160°C for curing, demoulding and trimming.
[0060] In order to further improve the verticality of the bag cage and the production efficiency of the bag cage, the bag cap of the bag cage of the present invention is integrally wound with the cage body structure. In order to meet the lateral and longitudinal strength requirements of the bag cage, the winding angle of the ribs and cross ribs on the mold can be adjusted, and the winding angle can be changed from 0° to 90° (the rib 1 and the cross rib 2 cannot be 0° or 90°). In order to further improve the overall compressive strength of th...
PUM
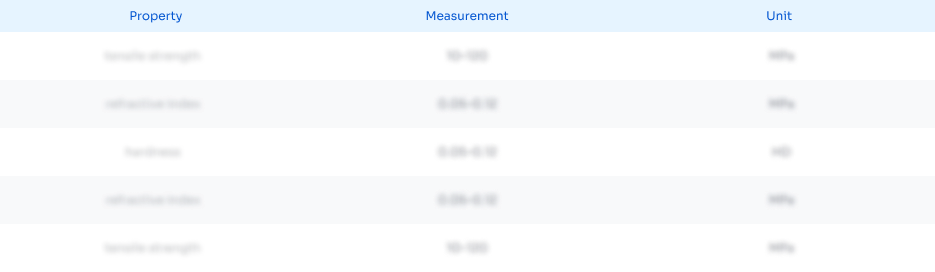
Abstract
Description
Claims
Application Information

- Generate Ideas
- Intellectual Property
- Life Sciences
- Materials
- Tech Scout
- Unparalleled Data Quality
- Higher Quality Content
- 60% Fewer Hallucinations
Browse by: Latest US Patents, China's latest patents, Technical Efficacy Thesaurus, Application Domain, Technology Topic, Popular Technical Reports.
© 2025 PatSnap. All rights reserved.Legal|Privacy policy|Modern Slavery Act Transparency Statement|Sitemap|About US| Contact US: help@patsnap.com