Control system of magnetorheological fluid load simulator and control method thereof
A load simulator, magnetorheological fluid technology, applied in the direction of program control system, general control system, control/regulation system, etc., can solve the maintenance work limitation of the load simulator, the limitation of load dynamic and time-varying characteristics, and can not be very good. to meet the control system and other problems
- Summary
- Abstract
- Description
- Claims
- Application Information
AI Technical Summary
Problems solved by technology
Method used
Image
Examples
Embodiment
[0059] A control system for a magnetorheological fluid load simulator, such as figure 1 As shown, it includes a microcontroller 1, a drive module 2, a magnetorheological fluid load simulator 3, a current detection module 4, a speed feedback module 5 and a power supply module 6, wherein:
[0060] Such as figure 2 As shown, the magneto-rheological fluid load simulator 3 includes a cylinder 301, a damping cylinder 302 arranged inside the cylinder 301, a transmission shaft 303 connected to the damping cylinder 302, and a cylinder wound around the damping cylinder 302. The excitation coil 304 on the cylinder 302, the side walls of the damping cylinder 302 and the cylinder 301 are made of magnetically conductive material, and the transmission shaft 303 extends outward from both ends of the cylinder 301 The working gap between the cylinder 301 and the damping cylinder 302 is filled with magnetorheological fluid 305, and the two ends of the cylinder 301 are provided with sealing mec...
PUM
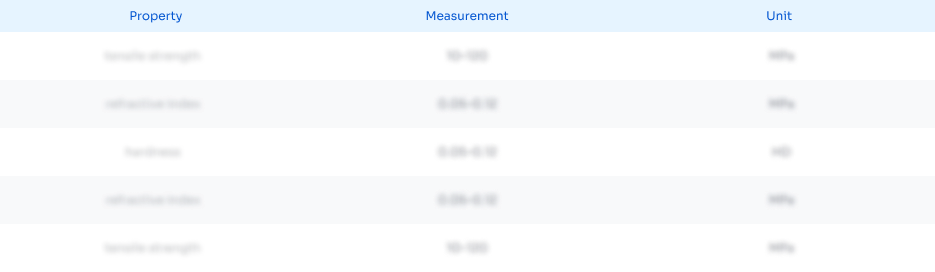
Abstract
Description
Claims
Application Information

- R&D
- Intellectual Property
- Life Sciences
- Materials
- Tech Scout
- Unparalleled Data Quality
- Higher Quality Content
- 60% Fewer Hallucinations
Browse by: Latest US Patents, China's latest patents, Technical Efficacy Thesaurus, Application Domain, Technology Topic, Popular Technical Reports.
© 2025 PatSnap. All rights reserved.Legal|Privacy policy|Modern Slavery Act Transparency Statement|Sitemap|About US| Contact US: help@patsnap.com