A production process of flame-retardant low-aldehyde solid wood composite floor
A solid wood composite floor, low-aldehyde technology, applied in the joining of wooden veneers, wood processing appliances, aldehyde/ketone condensation polymer adhesives, etc. and other problems, to achieve the effect of avoiding the gel effect of the polymerization reaction, low formaldehyde residue, and long flame retardant time.
- Summary
- Abstract
- Description
- Claims
- Application Information
AI Technical Summary
Problems solved by technology
Method used
Image
Examples
Embodiment 1
[0023] The production of modified urea-formaldehyde resin includes the following stages:
[0024] Pre-polymerization stage: Add formaldehyde to the reaction kettle, adjust the pH value to 2.6-3 with formic acid, add polyvinyl alcohol with 0.5-0.6% formaldehyde weight, add urea with 15% formaldehyde weight, heat up to 55-57°C, and keep warm for reaction 35~37min.
[0025] Polymerization stage: adjust the pH value of the reaction solution to 8.6-8.8, add urea with 25% formaldehyde weight, add melamine with 1.5% formaldehyde weight, raise the temperature to 96-98°C, and keep warm for 90-92 minutes.
[0026] Post-polymerization stage: add 45-50% urea by weight of formaldehyde solution, add 2.5% melamine by weight of formaldehyde solution, lower the reaction temperature to 65-69°C, react for 91-95 minutes, then cool down to room temperature to obtain low formaldehyde residue Urea-formaldehyde resin.
[0027] Hot plate process: apply glue to the solid wood composite floor, the amo...
Embodiment 2
[0029] First, synthesize PPU flame retardant: Add polyol phosphate (PAPE) into a four-necked flask equipped with a stirrer, reflux condenser and thermometer, and heat it to 80-82°C in a water bath. Weigh a certain amount of toluene diisocyanate (TDI-80) and pour it into a constant pressure funnel. Add the material within 1 hour, keep the heat for 2-2.1 hours, then add a small amount of hydroxyethyl acrylate (HEA) dissolved in p-hydroxyanisole into the reaction system, and drop a few drops of dibutyltin dilaurate (DBTDL ), react for 2 to 2.1 hours, add some ethyl acetate (EAC) to reduce the viscosity during the cooling process, and discharge the material to obtain a PPU flame retardant.
[0030] Next, carry out the glue mixing process: take 100 parts of the modified urea-formaldehyde resin obtained in Example 1, take 15 parts of the PPU flame retardant obtained in this embodiment, take 0.1 part of polydimethylsiloxane, stir and mix evenly, and then add 10 parts of calcium carb...
Embodiment 3
[0033] Get 104 parts of the modified urea-formaldehyde resin obtained in Example 1, get 17 parts of the PPU flame retardant obtained in Example 2, get 0.1 part of tributyl phosphate, stir and mix evenly, add 14 parts of kaolin, and grind with a three-roll mill After 30 minutes, a flame-retardant low-aldehyde urea-formaldehyde resin glue was obtained. The hot plate process is the same as in Example 2.
PUM
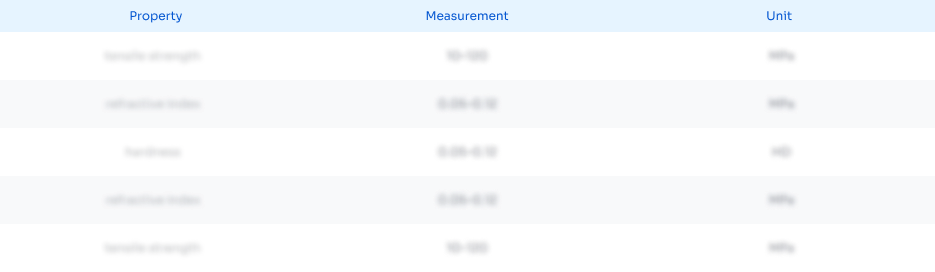
Abstract
Description
Claims
Application Information

- R&D
- Intellectual Property
- Life Sciences
- Materials
- Tech Scout
- Unparalleled Data Quality
- Higher Quality Content
- 60% Fewer Hallucinations
Browse by: Latest US Patents, China's latest patents, Technical Efficacy Thesaurus, Application Domain, Technology Topic, Popular Technical Reports.
© 2025 PatSnap. All rights reserved.Legal|Privacy policy|Modern Slavery Act Transparency Statement|Sitemap|About US| Contact US: help@patsnap.com