Car elastomer sound insulation material and manufacturing method thereof
A manufacturing method and body sound insulation technology, which is applied in the field of sound insulation materials and its manufacture, can solve the problems of poor mutual adhesion, low adhesion, and hazards of butyl rubber, and achieve good sound insulation effects, good physical properties, and noise reduction effects.
- Summary
- Abstract
- Description
- Claims
- Application Information
AI Technical Summary
Problems solved by technology
Method used
Image
Examples
Embodiment 1
[0027] A Xin'an-automobile front wall sound insulation product is set on the inner side of the car front wall and is a composite structure composed of PUR foam and elastomer sound insulation materials.
[0028] The manufacturing method of the elastic body sound insulation material comprises the following steps:
[0029] (1) Mixing in internal mixer: After weighing POE, PE, inorganic filler and extender oil according to the ratio of 70:30:280:20, put them into internal mixer for high-speed kneading, and exhaust once in the middle. After mixing for 6 minutes, the temperature reaches 130°C and then the rubber is removed.
[0030] (2) Mixing in the open mill: Put the above-mentioned rubber material on the open mill and roll it over and mix evenly. The roller heating temperature is 120°C.
[0031] (3) Making sheets: Put the mixed rubber material into the calender to output the sheet, the width of the door is 900mm, and the roller distance is adjusted to .
[0032] (4) Corona tre...
Embodiment 2
[0042] An elastomeric sound-insulating material for automobiles, which is processed by mixing thermoplastic elastomers POE, PE, inorganic filler barite powder and filler oil, wherein the weight ratio of POE, PE, barite powder and filler oil is 80:20:290:10, and the total number of parts of POE, PE, barite powder and extender oil is 400 parts. Extender oil is selected from technical grade white mineral oil.
[0043] A method for manufacturing an elastomeric sound-insulating material for automobiles, comprising the following steps:
[0044] (1) Mixing with internal mixer: After weighing POE, PE, barite powder and extender oil in a ratio of 80:20:290:10 by weight, and the total number of parts is 400 parts, put them into the compactor The mixer is kneaded at high speed, and exhausted twice in the middle to obtain the first rubber material, wherein the mixing time in the internal mixer is controlled at 5 minutes, and the bottom temperature of the mixing tank in the internal mixer...
Embodiment 3
[0051] An elastomeric sound-insulating material for automobiles, which is processed by mixing thermoplastic elastomers POE, PE, inorganic filler barite powder and filler oil, wherein the weight ratio of POE, PE, barite powder and filler oil is 75:25:285:15, and the total number of parts of POE, PE, barite powder and extender oil is 400 parts. Extender oil is selected from technical grade white mineral oil.
[0052] A method for manufacturing an elastomeric sound-insulating material for automobiles, comprising the following steps:
[0053](1) Mixing with internal mixer: After weighing POE, PE, barite powder and extender oil in a ratio of 75:25:285:15 in parts by weight, and the total number of parts is 400 parts, put them into the compactor The mixer kneads at a high speed, and exhausts air once in the middle to obtain the first rubber material. The mixing time in the internal mixer is controlled at 7 minutes, and the bottom temperature of the mixing tank in the internal mixer...
PUM
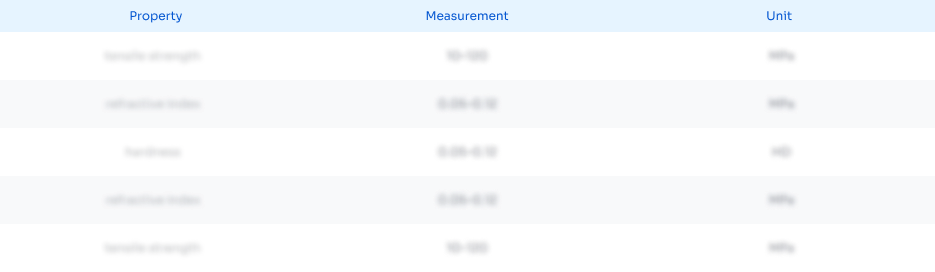
Abstract
Description
Claims
Application Information

- R&D
- Intellectual Property
- Life Sciences
- Materials
- Tech Scout
- Unparalleled Data Quality
- Higher Quality Content
- 60% Fewer Hallucinations
Browse by: Latest US Patents, China's latest patents, Technical Efficacy Thesaurus, Application Domain, Technology Topic, Popular Technical Reports.
© 2025 PatSnap. All rights reserved.Legal|Privacy policy|Modern Slavery Act Transparency Statement|Sitemap|About US| Contact US: help@patsnap.com