Method for preparing epoxy caryophyllene from heavy turpentine oil and separating longifolene
A technology of epoxy caryophyllene and heavy turpentine, which is applied in the purification/separation of hydrocarbons, chemical instruments and methods, hydrocarbons, etc., and can solve problems such as reducing the content of β-caryophyllene, hidden dangers in operation safety, and environmental pollution. Achieve good antibacterial and bactericidal activity, simple operation process, and mild reaction conditions
- Summary
- Abstract
- Description
- Claims
- Application Information
AI Technical Summary
Problems solved by technology
Method used
Image
Examples
Embodiment 1
[0044] In the 500ml reactor equipped with reflux condensation and constant temperature stirring device, add 60.0ml (56.0g) heavy turpentine oil (which contains 36.4g of longifolene, 178.0mmol; β-caryophyllene 10.4g, 51.0mmol), 100ml ethyl acetate, 0.6g catalyst Q 3 PMo 2 W 2 o 24 , 91.0mmol hydrogen peroxide, reacted at 35°C for 2.5h. After the reaction was completed, the conversion rates of β-caryophyllene and longifolene were respectively 98.1% and 0, and the yield of epoxycaryophyllene was 96.6%.
[0045] The reaction mixture was cooled to 15°C to allow the catalyst to fully precipitate and be recovered by filtration; the filtrate was allowed to stand still and the phases were separated to remove the water phase, and the organic phase was distilled under reduced pressure to recover the organic solvent; the residue was separated by fractional distillation under reduced pressure to obtain two oils Liquid products: longifolene (97.4% yield, 92.8% purity) and caryophyllene ...
Embodiment 2
[0047] In a 500ml reactor equipped with reflux condensation and constant temperature stirring device, add 60.0ml (56.0g) heavy turpentine, 100ml ethyl acetate, 0.6g catalyst Q 3 PW 4 o 24 , 91.0mmol hydrogen peroxide, reacted at 30°C for 1h. After the reaction is completed, the conversion rates of β-caryophyllene and longifolene are respectively 100% and 0.05% through gas chromatography analysis and detection, and the yield of epoxycaryophyllene is 95.8%.
[0048] After the reaction, the reaction mixture was cooled to 15°C, the catalyst was precipitated, filtered and recovered, the filtrate was evaporated under reduced pressure to recover the solvent, and the residue was fractionated under reduced pressure at a vacuum degree of 935Pa to obtain two oily liquid products : longifolene (yield 96.8%, purity 91.7%) and epoxy caryophyllene (yield 92.0%, purity 95.5%); add a small amount of crystal seeds to epoxy caryophyllene-like liquid, and place it at 15°C for precipitation Cry...
Embodiment 3
[0050] In a 500ml reactor equipped with reflux condensation and constant temperature stirring device, add 60.0ml (56.0g) heavy turpentine, 100ml ethyl acetate, 1.2g catalyst Q 3 PMo 4 o 24 , 91.0mmol hydrogen peroxide, reacted at 50°C for 12h. After the reaction was completed, the conversion rates of β-caryophyllene and longifolene were respectively 94.7% and 0, and the yield of epoxycaryophyllene was 94.9%.
[0051]After the reaction, the reaction mixture was cooled to 15°C, the catalyst was precipitated, filtered and recovered, the filtrate was evaporated under reduced pressure to recover the solvent, and the residue was fractionated under reduced pressure at a vacuum degree of 935Pa to obtain two oily liquid products : longifolene (yield 97.4%, purity 92.0%) and epoxy caryophyllene (yield 90.9%, purity 95.4%); add a small amount of crystal seeds to epoxy caryophyllene-like liquid, and place it at 15°C for precipitation Crystals, the crystals are collected by vacuum filtr...
PUM
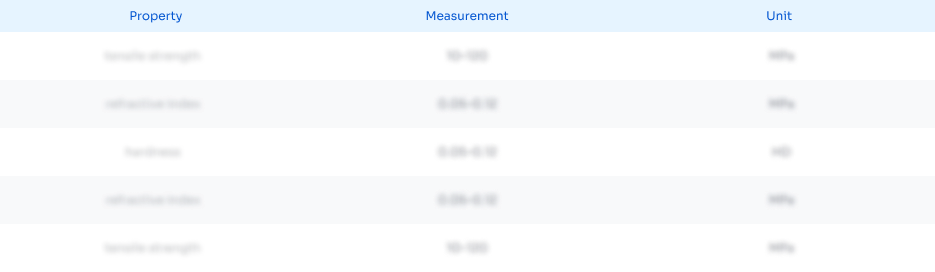
Abstract
Description
Claims
Application Information

- R&D
- Intellectual Property
- Life Sciences
- Materials
- Tech Scout
- Unparalleled Data Quality
- Higher Quality Content
- 60% Fewer Hallucinations
Browse by: Latest US Patents, China's latest patents, Technical Efficacy Thesaurus, Application Domain, Technology Topic, Popular Technical Reports.
© 2025 PatSnap. All rights reserved.Legal|Privacy policy|Modern Slavery Act Transparency Statement|Sitemap|About US| Contact US: help@patsnap.com