Firing technique of blue-and-white underglaze red
An underglaze red and blue-and-white technology is applied to the firing process of blue-and-white underglaze red. Even, brightly colored results
- Summary
- Abstract
- Description
- Claims
- Application Information
AI Technical Summary
Problems solved by technology
Method used
Examples
Embodiment 1
[0016] 1) Preparation of blanks and glazes:
[0017] The blank is composed of raw materials in the following weight percentages: SiO 2 70%, Al 2 o 3 20%, Fe 2 o 3 0.15%, CaO 0.3%, K 2 O 1.2%, Na 2 O 0.6%, MgO 0.4%, IL 7.35%;
[0018] The glaze consists of the following raw materials in weight percentage: SiO 2 75%, Al 2 o 3 15%, CaO 2%, K 2 O 2%, Na 2 O 3%, MgO 3%;
[0019] 2) Preparing the green body: making the blank into a green body, trimming, and drying for later use;
[0020] 3) Underglaze blue and white: use blue and copper red materials to draw patterns or write characters on the surface of the green body, and then perform glazing treatment and dry to form the blue and white green body;
[0021] 4) Firing: Put the blue and white body into the kiln, first control the kiln in an oxidizing atmosphere, raise the temperature to 300°C at a rate of 100°C / h, and then continue to heat up to 950°C at a rate of 150°C / h; then Control the kiln in a reducing atmosphere...
Embodiment 2
[0023] 1) Preparation of blanks and glazes:
[0024] The blank is composed of raw materials in the following weight percentages: SiO 2 75%, Al 2 o 3 15%, Fe 2 o 3 0.24%, CaO 0.5%, K 2 O 2%, Na 2 O 1.5%, MgO 0.7%, IL 6.86%;
[0025] The glaze consists of the following raw materials in weight percentage: SiO 2 80%, Al 2 o 3 15%, K 2 O 2%, Na 2 O 3%;
[0026] 2) Preparing the green body: making the blank into a green body, trimming, and drying for later use;
[0027] 3) Underglaze blue and white: use blue and copper red materials to draw patterns or write characters on the surface of the green body, and then perform glazing treatment and dry to form the blue and white green body;
[0028] 4) Firing: Put the blue and white body into the kiln, first control the kiln in an oxidizing atmosphere, raise the temperature to 300°C at a rate of 120°C / h, and then continue to heat up to 950°C at a rate of 200°C / h; then Control the kiln in a reducing atmosphere (when the tempera...
Embodiment 3
[0030] 1) Preparation of blanks and glazes:
[0031] The blank is composed of raw materials in the following weight percentages: SiO 2 72%, Al 2 o 3 18%, Fe 2 o 3 0.2%, CaO 0.4%, K 2 O 1.5%, Na 2 O 1%, MgO 0.5%, IL 6.4%;
[0032] The glaze consists of the following raw materials in weight percentage: SiO 2 78%, Al 2 o 3 14%, Fe 2 o 3 0.1%, CaO 0.5%, K 2 O 3%, Na 2 O 4%, MgO 0.4%;
[0033] 2) Preparing the green body: making the blank into a green body, trimming, and drying for later use;
[0034] 3) Underglaze blue and white: use blue and copper red materials to draw patterns or write characters on the surface of the green body, and then perform glazing treatment and dry to form the blue and white green body;
[0035] 4) Firing: Put the blue and white body into the kiln, first control the kiln in an oxidizing atmosphere, raise the temperature to 300°C at a rate of 110°C / h, and then continue to heat up to 950°C at a rate of 180°C / h; then Control the kiln in a re...
PUM
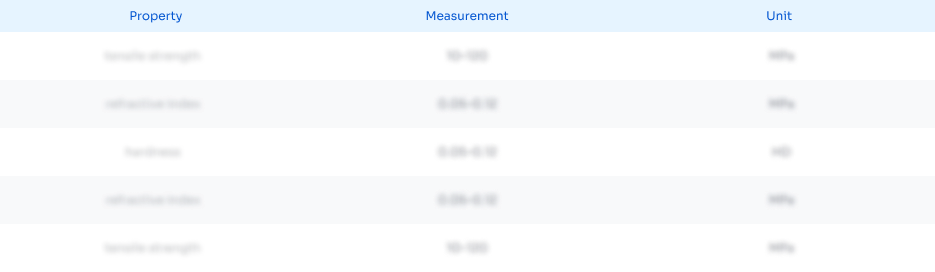
Abstract
Description
Claims
Application Information

- R&D
- Intellectual Property
- Life Sciences
- Materials
- Tech Scout
- Unparalleled Data Quality
- Higher Quality Content
- 60% Fewer Hallucinations
Browse by: Latest US Patents, China's latest patents, Technical Efficacy Thesaurus, Application Domain, Technology Topic, Popular Technical Reports.
© 2025 PatSnap. All rights reserved.Legal|Privacy policy|Modern Slavery Act Transparency Statement|Sitemap|About US| Contact US: help@patsnap.com