Ultrathin slurry sprinkling and glazing process
A slurry-spraying and ultra-thin technology, applied in the field of building bricks, can solve the problems of rough inkjet pattern, poor anti-fouling ability, low wear resistance, etc., and achieve the effect of smooth and delicate touch, bright color and improved processing speed.
- Summary
- Abstract
- Description
- Claims
- Application Information
AI Technical Summary
Problems solved by technology
Method used
Examples
Embodiment 1
[0028] The present invention claims to protect an ultra-thin glazing process, which comprises the following steps:
[0029] Step (1), prepare the porcelain tile bottom blank, and set it aside. The composition ratio of the bottom billet is as follows, loss on ignition: 5.02%; silicon dioxide: 35.45%; aluminum oxide: 35.96%; calcium oxide: 10.44%; magnesium oxide: 3.67%; Sodium: 0.29%; Zinc Oxide: 0.89%; Zirconia: 4.56%.
[0030] Step (2), preparing flour paste, for subsequent use. First prepare W glaze slurry, which is composed by weight percentage: high-temperature matt transparent wear-resistant frit A: 57-61%; sub-surface transparent glaze B: 39-43%; water: 40-42%; carboxymethyl fiber Sodium plain: 0.2-0.3%; Sodium tripolyphosphate: 0.3-0.38%; The processing fineness of W glaze slurry can be 325 mesh, and the sieve residue is 0.2-0.6%. Then use W glaze slurry to prepare ultra-thin pouring slurry L glaze, that is, composite glaze slurry. The ingredients ratio of L glaze is...
Embodiment 2
[0041] It is known in the field that the choice of abrasive tools directly affects the final matte effect, and the fineness of the abrasive in each polishing process is also crucial. If the fineness is too fine, the finish will be higher without matte effect. If it is too thick, the smoothness will be low. Although the tiles with matte effect can be produced at this time, the product has a strong graininess and is prone to serious scratches, which makes the product particularly not resistant to stains. Therefore, during polishing The abrasive tools in each process must be strictly selected, and the fineness of the abrasives should also be carefully considered to make it just right.
[0042] This embodiment is mainly aimed at further research and development of the polishing process in Example 1. In Example 2, the soft polishing in Example 1 is used as the polishing process, which specifically includes three steps. The grinding tool of the grinding tool is polished, wherein the...
PUM
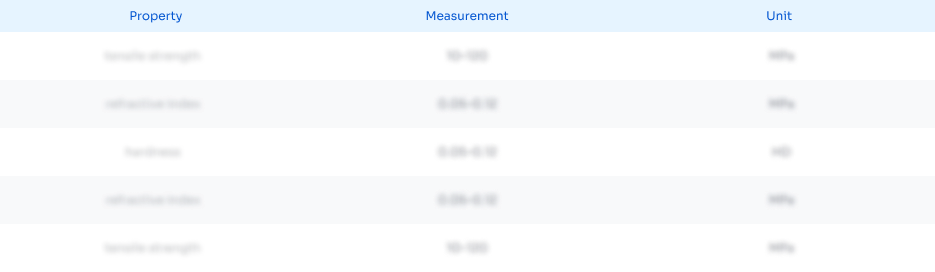
Abstract
Description
Claims
Application Information

- Generate Ideas
- Intellectual Property
- Life Sciences
- Materials
- Tech Scout
- Unparalleled Data Quality
- Higher Quality Content
- 60% Fewer Hallucinations
Browse by: Latest US Patents, China's latest patents, Technical Efficacy Thesaurus, Application Domain, Technology Topic, Popular Technical Reports.
© 2025 PatSnap. All rights reserved.Legal|Privacy policy|Modern Slavery Act Transparency Statement|Sitemap|About US| Contact US: help@patsnap.com