Stirring friction connecting device capable of reducing deformation and removing flashes
A technology of friction stirring and connecting devices, which is applied in welding equipment, non-electric welding equipment, metal processing, etc., can solve problems such as the distance between the fixture and the weld seam, poor butt joint, warping, etc., so as to reduce milling work and improve constraints , reduce the effect of secondary deformation
- Summary
- Abstract
- Description
- Claims
- Application Information
AI Technical Summary
Problems solved by technology
Method used
Image
Examples
Embodiment 1
[0032] to combine figure 1 and figure 2 Describe the implementation process. In this embodiment, the thickness of the workpiece to be welded is 2mm, the length of the stirring needle is 1.5mm, the amount of pressure during welding is 2mm, the vertical distance between the sleeve and the shaft shoulder is 0.5mm, the outer diameter of the sleeve is 65mm, and the inner diameter is 20mm, the thickness of the sleeve is 22.5mm. The height of the sleeve is 33.5mm. During the welding process, the stirring head, the large cylinder (8) and the bearing block (2) rotate around the axis, but the sleeve (5) does not rotate. After the welding starts, the workpiece moves at a constant speed in a certain direction , the sleeve (5) compresses the workpiece through the downward pressure transmitted by the pressure block (2), realizing the vertical constraint. After the welding starts, all the surrounding areas to be welded are fixed to ensure the smoothness of the welding process. In the la...
Embodiment 2
[0034] to combine figure 1 and figure 2Describe the implementation process. In this embodiment, the thickness of the workpiece to be welded is 1mm, the length of the stirring needle is 0.8mm, the amount of pressure during welding is 1mm, the vertical distance between the sleeve and the shaft shoulder is 0.2mm, the outer diameter of the sleeve is 65mm, and the inner diameter is 20mm, the thickness of the sleeve is 22.5mm. The height of the sleeve is 33.2mm. During the welding process, the stirring shaft (1), the large cylinder (8), and the pressure block (2) rotate around the axis, and the sleeve (5) does not rotate. After the welding starts, the workpiece moves along a certain direction Moving at a constant speed, the sleeve (5) presses the workpiece through the downward force transmitted by the pressure block (2) to achieve vertical restraint. After the welding starts, all the surrounding areas to be welded are fixed to ensure the smoothness of the welding process. At th...
PUM
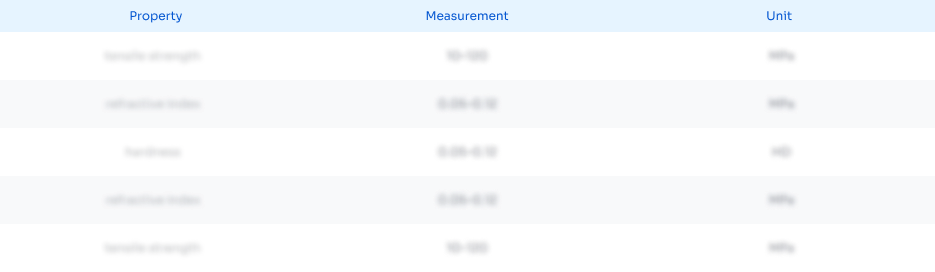
Abstract
Description
Claims
Application Information

- R&D
- Intellectual Property
- Life Sciences
- Materials
- Tech Scout
- Unparalleled Data Quality
- Higher Quality Content
- 60% Fewer Hallucinations
Browse by: Latest US Patents, China's latest patents, Technical Efficacy Thesaurus, Application Domain, Technology Topic, Popular Technical Reports.
© 2025 PatSnap. All rights reserved.Legal|Privacy policy|Modern Slavery Act Transparency Statement|Sitemap|About US| Contact US: help@patsnap.com