Integrated radioactive source welding chamber
A technology of radioactive source and welding chamber, applied in the field of integrated radioactive source welding chamber, can solve the problems of increased manufacturing cost, lack of installation and positioning, welding quality influence, etc., to achieve improved position accuracy and installation and positioning accuracy, simple and practical structure, rotating high precision effect
- Summary
- Abstract
- Description
- Claims
- Application Information
AI Technical Summary
Problems solved by technology
Method used
Image
Examples
Embodiment Construction
[0021] Embodiments of the present invention are described in detail as follows in conjunction with accompanying drawings:
[0022] like Figure 1 to Figure 8 As shown, an integrated radioactive source welding chamber includes an installation base plate 1, a welding chamber 2, an observation window assembly, a clamping guide assembly, a welding torch installation sealing assembly, and a heat dissipation double spring top plate assembly. The welding chamber 2 and the installation base plate 1 Fixed connection, the heat dissipation double spring top plate assembly is installed on the right end of the welding chamber 2, the welding torch installation sealing assembly is installed on the top of the welding chamber 2, the clamping guide assembly is installed on the left end of the welding chamber 2, and the welding chamber 2 The front and rear ends are provided with observation window components.
[0023] The heat dissipation double spring top plate assembly includes a heat dissipa...
PUM
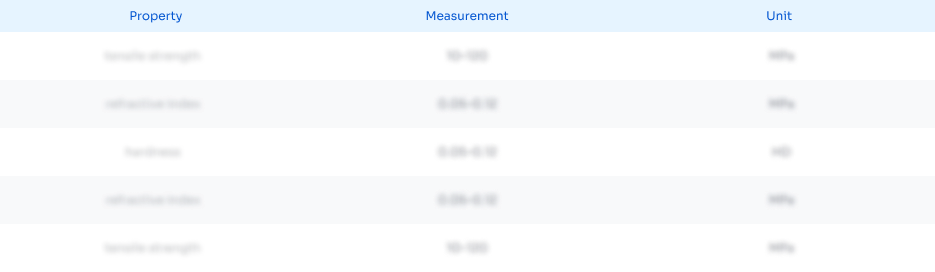
Abstract
Description
Claims
Application Information

- R&D
- Intellectual Property
- Life Sciences
- Materials
- Tech Scout
- Unparalleled Data Quality
- Higher Quality Content
- 60% Fewer Hallucinations
Browse by: Latest US Patents, China's latest patents, Technical Efficacy Thesaurus, Application Domain, Technology Topic, Popular Technical Reports.
© 2025 PatSnap. All rights reserved.Legal|Privacy policy|Modern Slavery Act Transparency Statement|Sitemap|About US| Contact US: help@patsnap.com