Multi-point forming method for whole aluminum alloy wall plate of aircraft
A technology of integral wallboard and multi-point forming, which is applied in metal processing, forming tools, metal processing equipment, etc., to achieve the effect of improving forming accuracy and improving forming ability
- Summary
- Abstract
- Description
- Claims
- Application Information
AI Technical Summary
Problems solved by technology
Method used
Image
Examples
Embodiment Construction
[0020] refer to image 3 It is a process flow chart of the multi-point forming method for an aluminum alloy aircraft integral wall panel of the present invention. The aluminum alloy aircraft integral panel is an aluminum alloy integral panel with I-shaped, T-shaped or J-shaped high ribs, and the structure of the ribs is Unidirectional distribution, grid structure or rice-shaped structure, the upper and lower multi-point molds 1 and 5, which can be quickly reconstructed, are used to form aluminum alloy aircraft with rib structure according to the planned deformation path Integral panel 3 divides the large target deformation into multiple steps non-uniformly, gradually changes the shape of the forming surface of the multi-point mold, and performs gradual counter-press forming, and finally obtains the required large-deformed aluminum alloy aircraft through the gradual accumulation of small deformations Integral wallboard 3, this method comprises the following steps:
[0021] Ste...
PUM
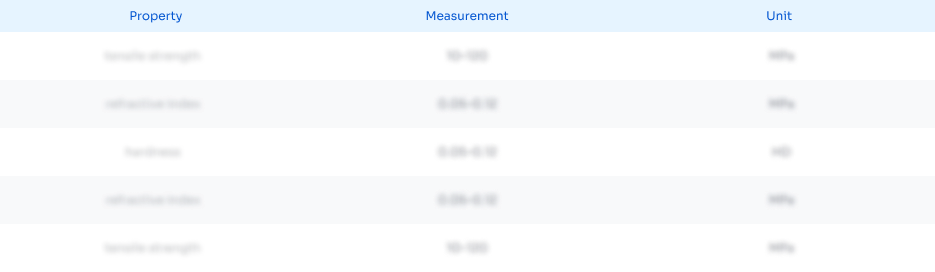
Abstract
Description
Claims
Application Information

- R&D
- Intellectual Property
- Life Sciences
- Materials
- Tech Scout
- Unparalleled Data Quality
- Higher Quality Content
- 60% Fewer Hallucinations
Browse by: Latest US Patents, China's latest patents, Technical Efficacy Thesaurus, Application Domain, Technology Topic, Popular Technical Reports.
© 2025 PatSnap. All rights reserved.Legal|Privacy policy|Modern Slavery Act Transparency Statement|Sitemap|About US| Contact US: help@patsnap.com