Modified composite oxide catalyst and modification method
A catalyst and mixture technology, which is applied in the field of improving the activity of composite oxide catalysts, can solve the problems of low catalyst activity, low catalyst selectivity, inability to propylene and high acrylic acid yield, etc.
- Summary
- Abstract
- Description
- Claims
- Application Information
AI Technical Summary
Problems solved by technology
Method used
Image
Examples
preparation example Construction
[0056] The catalyst precursor of the present invention can be prepared by common methods known in the art. In an example of the present invention, the preparation method of described catalyst precursor comprises:
[0057] (i) Dissolve Mo, V and W sources in water at 70-100°C to obtain A solution, and dissolve Cu, X and Y sources in water at 60-80°C to obtain B solution;
[0058] (ii) Pour solution B into solution A at 40-80°C to obtain solution C, directly add component Z to the solution and stir and mix evenly to obtain solution D, and dry solution D to obtain catalyst powder; or dry solution C first The powder is obtained, and then the powder is mixed with the Z component uniformly to obtain the catalyst powder.
[0059] Drying is static drying at 90-200°C or spray drying at an inlet temperature of 270-350°C and an outlet temperature of 120-160°C.
[0060] The catalyst carrier of the present invention can also be purchased from the market, for example, it can be purchased ...
Embodiment 1
[0086] Preparation of catalyst precursor
[0087] Add 65.1g ammonium molybdate, 11.8g ammonium metatungstate and 16.6g ammonium metavanadate to 300g water at 90°C, stir and dissolve to obtain A solution;
[0088] Add 5g of antimony trioxide, 2g of strontium nitrate and 12g of copper nitrate into 50g of water at 60°C, stir and dissolve to obtain solution B;
[0089] Pour B solution into A solution at 60°C to obtain C solution, and spray C solution at an inlet temperature of 270°C and an outlet temperature of 120°C to obtain a dry powder;
[0090] Take 30g of dry powder and 30g of silicon powder and mix evenly to obtain catalyst powder.
[0091] Improve the activity of catalyst precursors
[0092] Add 15g of sulfolane to 60g of the catalyst precursor powder prepared above and mix well; dry at 150°C in air for 12 hours; ) in an atmosphere of 380 ° C for 5 hours to obtain the catalyst.
[0093] The performance of the obtained catalyst was evaluated by the above method, and...
Embodiment 2~4
[0095] The same experimental method as in Example 1 was adopted, except that the amount of sulfolane shown in Table 1 was used in the method for improving the activity of the composite oxide catalyst.
[0096] The performance of the obtained catalyst was evaluated by the above method, and the results are shown in Table 1.
PUM
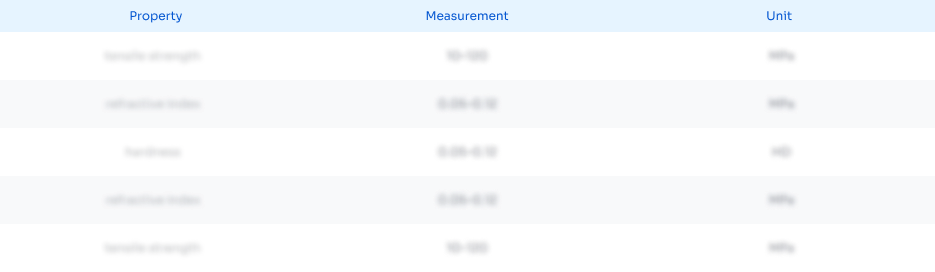
Abstract
Description
Claims
Application Information

- Generate Ideas
- Intellectual Property
- Life Sciences
- Materials
- Tech Scout
- Unparalleled Data Quality
- Higher Quality Content
- 60% Fewer Hallucinations
Browse by: Latest US Patents, China's latest patents, Technical Efficacy Thesaurus, Application Domain, Technology Topic, Popular Technical Reports.
© 2025 PatSnap. All rights reserved.Legal|Privacy policy|Modern Slavery Act Transparency Statement|Sitemap|About US| Contact US: help@patsnap.com