Ultrasonic welding method and device
An ultrasonic welding and ultrasonic technology, applied in welding equipment, non-electric welding equipment, program-controlled manipulators, etc., can solve the problems of poor welding quality, low welding position positioning accuracy, low manual operation efficiency, etc., to expand application fields and improve automation. degree of effect
- Summary
- Abstract
- Description
- Claims
- Application Information
AI Technical Summary
Problems solved by technology
Method used
Image
Examples
Embodiment Construction
[0020] The specific implementation of the ultrasonic welding method of the present invention will be described in detail below in conjunction with the accompanying drawings.
[0021] Such as figure 1 Shown, a method for ultrasonic welding, comprising steps:
[0022] S110. Call the preset motion track parameters and send them to the robot controller, wherein the robot controller is used to control the motion of the robot through the servo driver according to the motion track parameters;
[0023] S120. Call the preset ultrasonic welding parameters that match the motion track parameters, and send them to the ultrasonic welding power supply, wherein the ultrasonic welding power supply is used to adjust the ultrasonic waves output to the welding head according to the ultrasonic welding parameters, and the welding machine The head is mounted on the robot.
[0024] Step S110 and step S120 have no sequence and can be performed simultaneously. The robot controller is used to control...
PUM
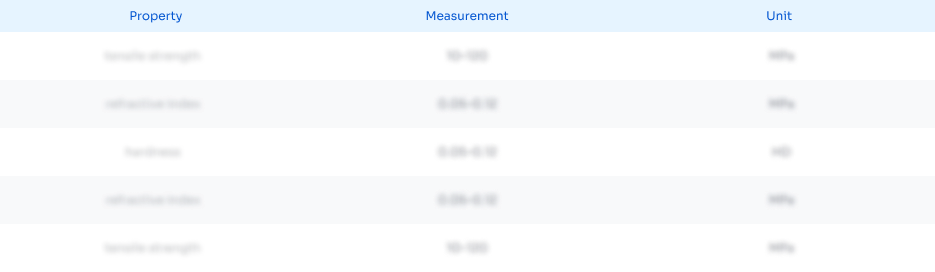
Abstract
Description
Claims
Application Information

- R&D
- Intellectual Property
- Life Sciences
- Materials
- Tech Scout
- Unparalleled Data Quality
- Higher Quality Content
- 60% Fewer Hallucinations
Browse by: Latest US Patents, China's latest patents, Technical Efficacy Thesaurus, Application Domain, Technology Topic, Popular Technical Reports.
© 2025 PatSnap. All rights reserved.Legal|Privacy policy|Modern Slavery Act Transparency Statement|Sitemap|About US| Contact US: help@patsnap.com