Continuous growth method of thin films at high temperature and under vacuum conditions
A thin film and vacuum technology, applied in the field of similar devices, can solve the problems of restricting film growth efficiency, small growth size of single film, long film growth period, etc.
- Summary
- Abstract
- Description
- Claims
- Application Information
AI Technical Summary
Problems solved by technology
Method used
Image
Examples
Embodiment
[0021] Embodiment: continuous growth of graphene film under high temperature and vacuum:
[0022] 1. Close the slide valves (2), (3), and (4), pump the growth chamber (8) and the cooling chamber (9) to the required vacuum degree, and the heating member (6) heats the space surrounded by it to High temperature (1000 degrees Celsius) required for thin film growth;
[0023] 2. Open the gate valve (1), push the shelf (7) carrying the multi-layer Cu substrate into the preparation chamber (5) through the slide rail (10), close the gate valve (1), and evacuate to and When the vacuum degree of the growth chamber (8) is equal, open the slide valve (2), push the shelf (7) into the high-temperature zone, and the reaction gas (methane + hydrogen) enters the growth chamber (8) through the micro-leakage valve (18). During the film growth process, the preparatory chamber (5) can be inflated to atmospheric pressure at the same time, and then the second batch of shelves (19) loaded with substr...
PUM
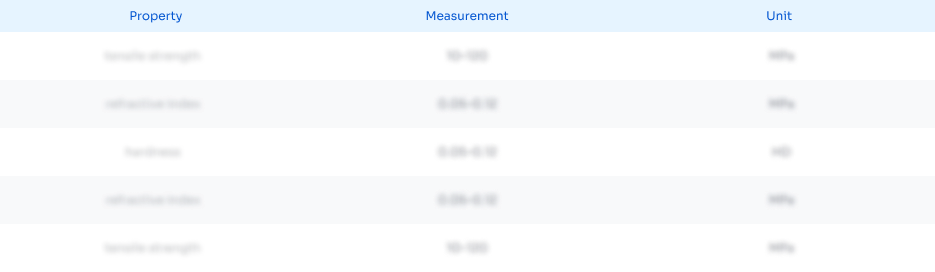
Abstract
Description
Claims
Application Information

- R&D Engineer
- R&D Manager
- IP Professional
- Industry Leading Data Capabilities
- Powerful AI technology
- Patent DNA Extraction
Browse by: Latest US Patents, China's latest patents, Technical Efficacy Thesaurus, Application Domain, Technology Topic, Popular Technical Reports.
© 2024 PatSnap. All rights reserved.Legal|Privacy policy|Modern Slavery Act Transparency Statement|Sitemap|About US| Contact US: help@patsnap.com