Super wear-resistant compound vertical mill roller shell and manufacture method thereof
A vertical grinding roller sleeve, super wear-resistant technology, applied in the casting field, can solve the problems of peeling off blocks, high maintenance costs, etc., to achieve the effect of eliminating blocks and shortening the production cycle
- Summary
- Abstract
- Description
- Claims
- Application Information
AI Technical Summary
Problems solved by technology
Method used
Image
Examples
Embodiment 1
[0042] Such as figure 1 Shown is a cross-sectional view of a super wear-resistant composite vertical mill roll sleeve according to a specific embodiment of the present invention, and the super wear-resistant composite vertical grinder roll sleeve includes a super wear-resistant outer layer 1 and a high-toughness inner layer 2, the outer layer is metallurgically cast super wear-resistant cast iron, the outer layer has carbide sites with a content greater than 35%, and the inner layer is high-toughness medium-carbon low-alloy steel. That is, the outer layer is a wear-resistant layer, and the inner layer is a high-toughness layer.
[0043] Wherein, the carbide points are point-like carbides formed by alloying elements, and the average microhardness of the carbide points is ≥HV2700.
[0044] Preferably, the carbide points are dispersed in the super wear-resistant cast iron.
[0045] Further preferably, the super wear-resistant outer layer is metallurgically combined with the hig...
Embodiment 2
[0049] In this embodiment, the present invention also discloses a preparation method that can be used to manufacture the super wear-resistant composite vertical mill roll sleeve described in Embodiment 1. see figure 2 , shows the flow chart of the preparation method of the super wear-resistant composite vertical mill roll sleeve, see image 3 , which shows a schematic diagram of the pouring system for making super wear-resistant composite vertical mill roll sleeves.
[0050] Described preparation method comprises the steps:
[0051] Step 1. Making a metal mold, wherein the metal mold adopts static casting, and the material is gray iron. Process and produce metal molds according to the requirements of the drawings;
[0052] Step 2. Make the inner layer: use high-toughness medium-carbon low-alloy steel as the inner layer material. The outer surface of the inner layer is processed with 2mm sharp lines, and the inner layer is heated to 930°C and kept for 3 hours;
[0053] Ste...
PUM
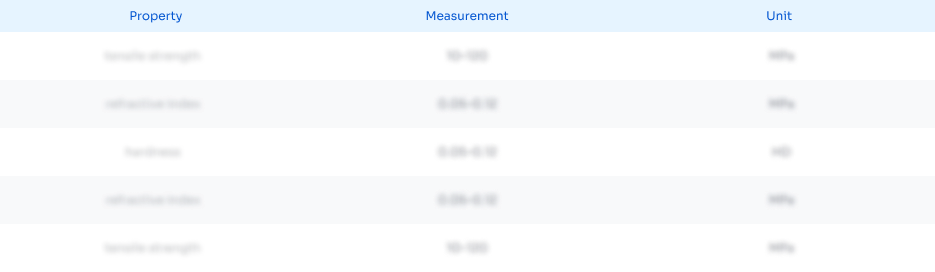
Abstract
Description
Claims
Application Information

- R&D Engineer
- R&D Manager
- IP Professional
- Industry Leading Data Capabilities
- Powerful AI technology
- Patent DNA Extraction
Browse by: Latest US Patents, China's latest patents, Technical Efficacy Thesaurus, Application Domain, Technology Topic, Popular Technical Reports.
© 2024 PatSnap. All rights reserved.Legal|Privacy policy|Modern Slavery Act Transparency Statement|Sitemap|About US| Contact US: help@patsnap.com