Welding process of aluminum alloy car body chassis for subway
An aluminum alloy car body and welding process technology, applied in the field of aluminum alloy welding, can solve the problems of large residual stress after welding, large gap between welds, welding deformation, etc., shorten the relative length of the weld, improve the accuracy of the weld, The effect of improving welding performance
- Summary
- Abstract
- Description
- Claims
- Application Information
AI Technical Summary
Problems solved by technology
Method used
Image
Examples
Embodiment Construction
[0050] The preferred embodiments of the present invention will be described in detail below with reference to the accompanying drawings.
[0051] As shown in the figure, the welding process of the aluminum alloy car body chassis for the subway in this embodiment mainly includes the following steps:
[0052] A. The bottom frame is installed:
[0053] 1) Fix the corbel 1 and the anchor 2 on the underframe assembly welding tooling, align the center of the anchor 2 and the corbel 1, and perform spot-fixing; in order to facilitate the welding of other welds, after the spot-fixing is completed, you can Cut the part where the lower cover plate is connected to the corbel.
[0054] 2) Fit the two side beams 3 correspondingly to both sides of the corbel 1 on the formal tooling, adjust the position of the side beams 3 and press them tightly.
[0055] 3) Preheat the welding seam 15HV between the connecting beam on the traction 2 and the corbel 1 and weld, the preheating temperature is 8...
PUM
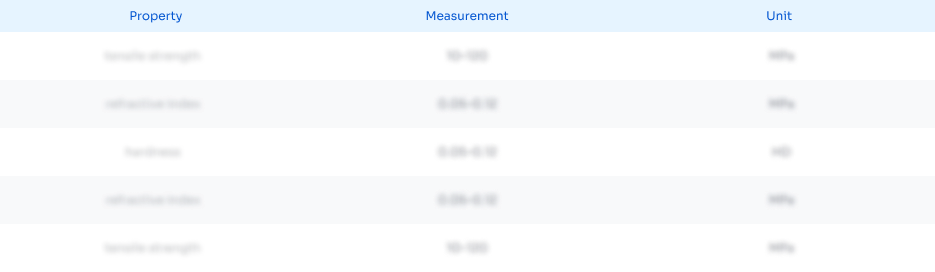
Abstract
Description
Claims
Application Information

- R&D
- Intellectual Property
- Life Sciences
- Materials
- Tech Scout
- Unparalleled Data Quality
- Higher Quality Content
- 60% Fewer Hallucinations
Browse by: Latest US Patents, China's latest patents, Technical Efficacy Thesaurus, Application Domain, Technology Topic, Popular Technical Reports.
© 2025 PatSnap. All rights reserved.Legal|Privacy policy|Modern Slavery Act Transparency Statement|Sitemap|About US| Contact US: help@patsnap.com