Vertical finish-milling machine
A precision milling machine, vertical technology, applied in milling machines, milling machine equipment, metal processing machinery parts, etc., can solve the problems of small effective distance, small workpiece range, high machining accuracy, etc., to increase the longitudinal working distance, increase machining range, the effect of increasing the machining accuracy
- Summary
- Abstract
- Description
- Claims
- Application Information
AI Technical Summary
Problems solved by technology
Method used
Image
Examples
Embodiment Construction
[0029] The present invention is further described in conjunction with the following examples.
[0030] Such as figure 1 As shown, the vertical fine milling machine of the present invention includes a gantry column 100 , a beam 200 arranged on the gantry column 100 , a headstock mechanism 300 and a worktable mechanism 400 installed on the beam 200 . Among them: such as figure 2 , image 3 , Figure 4 with Figure 5As shown, a spindle box 310, a spindle servo motor 311, a ram 320, a ram motor 321, a pair of balance cylinders (left balance cylinder 330, right balance cylinder 333) and a carriage 340; the spindle box 310 is fixed on the ram 20, the milling cutter of the fixed finish milling machine is installed on the spindle box 310; the spindle servo motor 311 is fixed on the spindle box 310 and provides driving force for the milling cutter; the ram 320 is arranged in a cuboid shape, and the carriage 340 is provided with a receiving groove 341, the ram 20 is arranged in th...
PUM
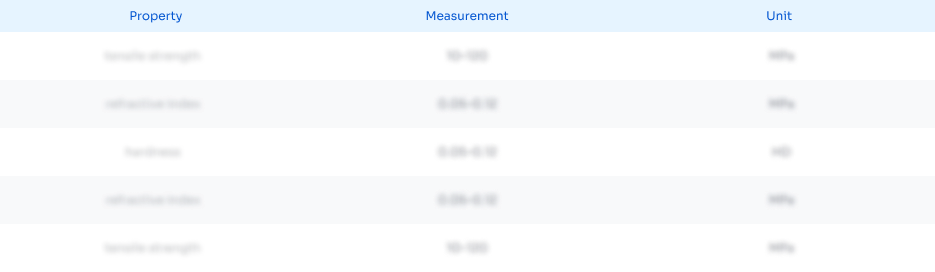
Abstract
Description
Claims
Application Information

- R&D
- Intellectual Property
- Life Sciences
- Materials
- Tech Scout
- Unparalleled Data Quality
- Higher Quality Content
- 60% Fewer Hallucinations
Browse by: Latest US Patents, China's latest patents, Technical Efficacy Thesaurus, Application Domain, Technology Topic, Popular Technical Reports.
© 2025 PatSnap. All rights reserved.Legal|Privacy policy|Modern Slavery Act Transparency Statement|Sitemap|About US| Contact US: help@patsnap.com