Energy-saving preparation technology of high-quality glucose powder
A technology of glucose powder and preparation process, which is applied in the direction of sustainable manufacturing/processing, chemical industry, climate sustainability, etc. It can solve the problems of difficult separation of crystals and mother liquor, high energy consumption of the system, and time-consuming operation, so as to avoid losses and The production of toxic substances, the effect of sufficient separation, and the effect of reducing the content of miscellaneous sugars
- Summary
- Abstract
- Description
- Claims
- Application Information
AI Technical Summary
Problems solved by technology
Method used
Examples
Embodiment 1
[0024]Get the starch, add process water to adjust the size, control the Baume degree of the starch milk after the size adjustment to be 18, adjust the pH value of the starch milk to 4.8, add liquefying enzyme (i.e. α-amylase) to the starch milk to liquefy, The amount of liquefaction enzyme added is 0.40kg / t starch dry basis. The starch milk is sprayed and liquefied by the liquefaction injector. The injection temperature is 120°C. The feed liquid enters the high temperature maintenance tank for 3 minutes to kill the enzyme. The pH value of the liquefied liquid is controlled at 5.0. The DE value is 14%. After heat exchange, the pH of the liquefied liquid was adjusted to 4.0, and 0.35 kg / t of dry-based saccharification enzyme was added for saccharification, which was kept for 48 hours with intermittent stirring during the process. The DE value was 98.2%, and the glucose content was 96.1%. The above feed liquid is subjected to plate and frame filtration, and the filtrate is subjec...
Embodiment 2
[0026] Get the starch, add process water to adjust the size, control the Baume degree of the starch milk after the size adjustment to be 15, adjust the pH value of the starch milk to 5.0, add liquefying enzyme (i.e. α-amylase) to the starch milk to liquefy, The amount of liquefying enzyme added is 0.35kg / t starch dry basis. The starch milk is sprayed and liquefied through the liquefaction injector. The injection temperature is 105°C. The feed liquid enters the high temperature maintenance tank and keeps for 3 minutes to kill the enzyme. The pH value of the liquefied liquid is controlled at 5.5. The DE value is 19%. After heat exchange, the pH of the liquefied liquid was adjusted to 4.5, and 0.40 kg / t of dry-based carbohydrase was added for saccharification. The heat preservation was carried out for 48 hours, with intermittent stirring during the process. The DE value was 98.1%, and the glucose content was 96.0%. The above-mentioned feed liquid is subjected to plate and frame f...
Embodiment 3
[0028] Get starch, add process water to carry out pulping, control the Baume degree of starch milk after pulping to be 20, adjust the pH value of starch milk to 6.0, add liquefaction enzyme (i.e. α-amylase) to starch milk, carry out liquefaction, The amount of liquefaction enzyme added is 0.30kg / t starch dry basis. The starch milk is sprayed and liquefied by the liquefaction injector. The injection temperature is 135°C. The feed liquid enters the high temperature maintenance tank for 3 minutes to kill the enzyme. The pH value of the liquefied liquid is controlled at 6.0. The DE value is 17%. After heat exchange, the pH of the liquefied liquid was adjusted to 5.0, and 0.45 kg / t of dry-based carbohydrase was added for saccharification. The heat preservation was carried out for 48 hours, with intermittent stirring during the process. The DE value was 98.2%, and the glucose content was 96.1%. The above feed liquid is subjected to plate and frame filtration, and the filtrate is sub...
PUM
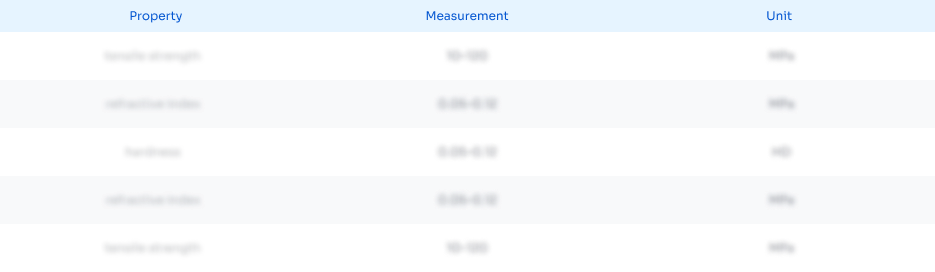
Abstract
Description
Claims
Application Information

- Generate Ideas
- Intellectual Property
- Life Sciences
- Materials
- Tech Scout
- Unparalleled Data Quality
- Higher Quality Content
- 60% Fewer Hallucinations
Browse by: Latest US Patents, China's latest patents, Technical Efficacy Thesaurus, Application Domain, Technology Topic, Popular Technical Reports.
© 2025 PatSnap. All rights reserved.Legal|Privacy policy|Modern Slavery Act Transparency Statement|Sitemap|About US| Contact US: help@patsnap.com