High-pressure-resistant rubber
A high-pressure and rubber technology, applied in the field of high-pressure rubber, can solve problems such as poor high pressure resistance, and achieve the effects of good heat resistance, high air tightness and excellent aging resistance
- Summary
- Abstract
- Description
- Claims
- Application Information
AI Technical Summary
Problems solved by technology
Method used
Examples
Embodiment 1
[0017] This high-pressure resistant rubber uses the following weights of raw materials:
[0018] Ethylene-propylene rubber: 80 kg; NBR: 17 kg; Chlorine ether rubber: 3 kg; stearic acid: 10 kg; carbon black: 30 kg; dithiocarbamate: 10 kg; polyethylene wax: 10 kg kg; paraffin: 15 kg; vulcanized resin: 15 kg;
[0019] A. The first mixing: Add ethylene propylene rubber, nitrile rubber, and epichlorohydrin rubber into the internal mixer, then add stearic acid, dithiocarbamate, polyethylene wax and carbon black, and then start the internal mixer Carry out the first mixing, the time is 130 seconds, and the temperature is 130°C;
[0020] B. The second mixing: Add paraffin to the internal mixer in step A and mix again, the time is 62 seconds, the temperature is 78 ° C, and then cooling and debinding;
[0021] C. Vulcanization: discharge the rubber in step B to the tablet press, then add vulcanized resin for kneading, the time is 120 seconds, and the tablet is ready.
Embodiment 2
[0023] This high-pressure resistant rubber uses the following weights of raw materials:
[0024] Ethylene-propylene rubber: 70 kg; NBR: 25 kg; Chlorine ether rubber: 5 kg; Stearic acid: 2 kg; Carbon black: 15 kg; Dithiocarbamate: 2 kg; Polyethylene wax: 2 kilograms; paraffin: 3 kilograms; vulcanized resin: 12 kilograms; all the other are identical with embodiment one.
Embodiment 3
[0026] This high-pressure resistant rubber uses the following weights of raw materials:
[0027] Ethylene-propylene rubber: 78 kg; NBR: 19 kg; Chlorine ether rubber: 3.8 kg; Stearic acid: 3 kg; Carbon black: 27 kg; Dithiocarbamate: 8 kg; Polyethylene wax: 8 kilograms; paraffin: 14 kilograms; vulcanized resin: 14.5 kilograms; All the other are identical with embodiment one.
PUM
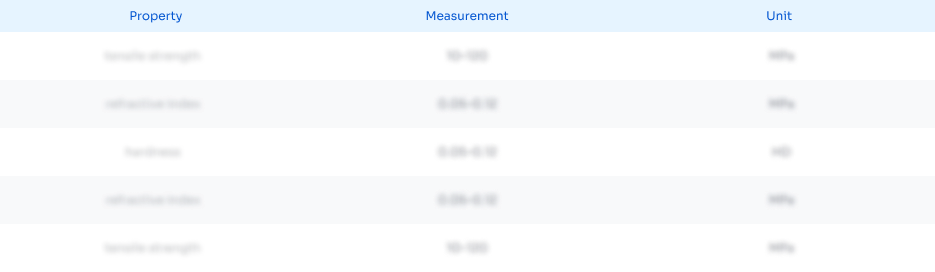
Abstract
Description
Claims
Application Information

- Generate Ideas
- Intellectual Property
- Life Sciences
- Materials
- Tech Scout
- Unparalleled Data Quality
- Higher Quality Content
- 60% Fewer Hallucinations
Browse by: Latest US Patents, China's latest patents, Technical Efficacy Thesaurus, Application Domain, Technology Topic, Popular Technical Reports.
© 2025 PatSnap. All rights reserved.Legal|Privacy policy|Modern Slavery Act Transparency Statement|Sitemap|About US| Contact US: help@patsnap.com