Piezoelectric linear motor and working method thereof
A technology of linear motor and piezoelectric actuation, applied in piezoelectric effect/electrostrictive or magnetostrictive motors, generators/motors, electrical components, etc. There is a large difference between thrust and pull, etc., to achieve the effect of light weight, fast response and high precision
- Summary
- Abstract
- Description
- Claims
- Application Information
AI Technical Summary
Problems solved by technology
Method used
Image
Examples
Embodiment Construction
[0036] The present invention will be further described below in conjunction with the accompanying drawings and specific embodiments.
[0037] Such as figure 1 , figure 2 As shown, the piezoelectric linear motor provided by the present invention is composed of a bidirectional force output mechanism a, a clamping mechanism b, a drive mechanism c, and a bottom plate 1, wherein the force output end of the bidirectional force output mechanism and the clamping mechanism pass through an output shaft a8 Connection, the clamping mechanism is connected with the driving mechanism of the clamping mechanism through a gear pair, and the described two-way force output mechanism, the clamping mechanism, and the driving mechanism of the clamping mechanism are all fixedly connected to the base plate.
[0038] A specific structure of the two-way force output mechanism a is as follows: image 3 , Figure 4 As shown, it includes four piezoelectric actuators a11, a12, a13, a14, two movable prel...
PUM
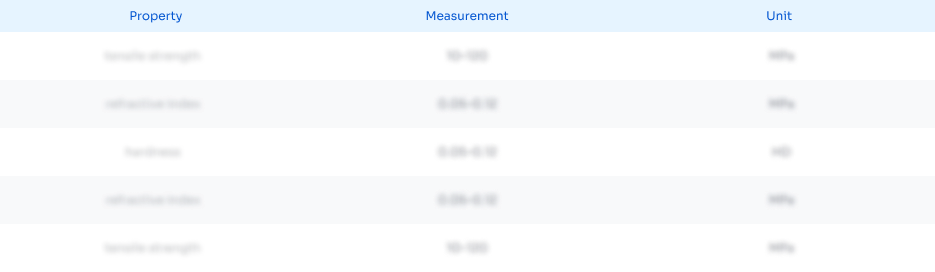
Abstract
Description
Claims
Application Information

- R&D
- Intellectual Property
- Life Sciences
- Materials
- Tech Scout
- Unparalleled Data Quality
- Higher Quality Content
- 60% Fewer Hallucinations
Browse by: Latest US Patents, China's latest patents, Technical Efficacy Thesaurus, Application Domain, Technology Topic, Popular Technical Reports.
© 2025 PatSnap. All rights reserved.Legal|Privacy policy|Modern Slavery Act Transparency Statement|Sitemap|About US| Contact US: help@patsnap.com