Novel magnetic gear for two-way air-gap field
A technology of air-gap magnetic field and magnetic gear, which is applied in the field of magnetic gear with a new bidirectional air-gap magnetic field, can solve the problems of magnetic path difference, low transmission torque and efficiency, low torque density, etc., and achieve the elimination of friction loss and reliability High, high transmission efficiency effect
- Summary
- Abstract
- Description
- Claims
- Application Information
AI Technical Summary
Problems solved by technology
Method used
Image
Examples
Embodiment Construction
[0034] The present invention will be described in further detail below in conjunction with the accompanying drawings and specific embodiments.
[0035] like Figure 1 ~ Figure 3 As shown, the present invention includes a stator casing 10 and a driving wheel coaxially installed in the stator casing 10, a driven wheel and a magnetic modulation grid 5, and the driving wheel and the driven wheel are respectively installed at two ends of the magnetic modulation grid 5, and the magnetic modulation The stator housing 10 is installed around the grid 5, the driving wheel and the driven wheel are both disc-shaped, there are gaps between the magnetic adjustment grid 5 and the driving wheel and the driven wheel respectively, and the center of the driving wheel inner ring 4 is provided with an input shaft 3 , P 1 For the driving wheel permanent magnet 1 of tangential magnetization, the driving wheel magnetization block 2 is installed between two adjacent driving wheel permanent magnets 1;...
PUM
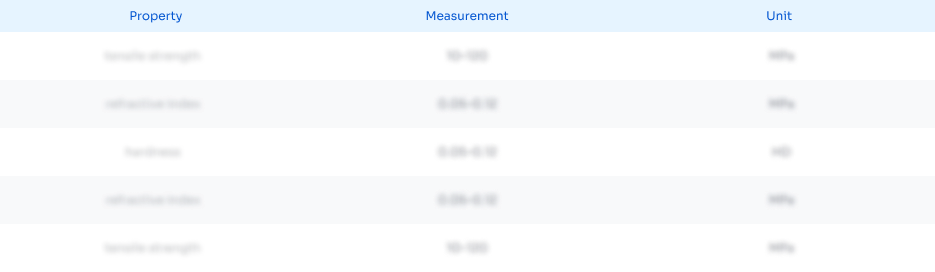
Abstract
Description
Claims
Application Information

- Generate Ideas
- Intellectual Property
- Life Sciences
- Materials
- Tech Scout
- Unparalleled Data Quality
- Higher Quality Content
- 60% Fewer Hallucinations
Browse by: Latest US Patents, China's latest patents, Technical Efficacy Thesaurus, Application Domain, Technology Topic, Popular Technical Reports.
© 2025 PatSnap. All rights reserved.Legal|Privacy policy|Modern Slavery Act Transparency Statement|Sitemap|About US| Contact US: help@patsnap.com