Method adopting PECVD for preparing back passivation film layer of solar back passivation battery
A technology of back passivation and solar energy, which is applied in the direction of circuits, photovoltaic power generation, electrical components, etc., can solve the problems of increasing the cost of back passivation batteries, high safety level requirements, and potential safety hazards, so as to improve the surface passivation effect and enhance Long-wave response and less production process
- Summary
- Abstract
- Description
- Claims
- Application Information
AI Technical Summary
Problems solved by technology
Method used
Image
Examples
Embodiment 1
[0014] A method for preparing a back passivation film layer of a solar back passivation battery using PECVD equipment provided in this embodiment comprises the following steps:
[0015] 1). Pretreatment of the original silicon wafer, the pretreatment includes the processes of texturing, diffusion and etching in the battery process;
[0016] 2). Use PECVD equipment to plate the back passivation film on the etching surface. The bottom layer is SiOx layer 1, the refractive index is 1.50, and the thickness of the film layer is 45nm; the upper layer is a single layer of SiN x Layer 2, the refractive index is 2.05, and the film thickness is 150nm;
[0017] 3). Use PECVD equipment to coat the diffusion surface, and use traditional battery printing technology to print the back electrode, aluminum back field, positive grid line and positive electrode after the back laser engraving, and sinter;
[0018] After testing, it is found that the photoelectric conversion efficiency of the back...
Embodiment 2
[0023] A method for preparing a back passivation film layer of a solar back passivation battery using PECVD equipment provided in this embodiment comprises the following steps:
[0024] 1). Pretreatment of the original silicon wafer, the pretreatment includes the processes of texturing, diffusion and etching in the battery process;
[0025] 2). Use PECVD equipment to plate the back passivation film on the etching surface. The bottom layer is SiOx layer 1, the refractive index is 1.60, and the film thickness is 90nm; the upper layer is double-layer SiN x Layer 2, the refractive index of SiN near the SiOx layer is 2.05, the film thickness is 50nm, the outermost layer SiNx has a refractive index of 2.0, and the film thickness is 50nm;
[0026] 3). Use PECVD equipment to coat the diffusion surface, and use traditional battery printing technology to print the back electrode, aluminum back field, positive grid line and positive electrode after the back laser engraving, and sinter; ...
PUM
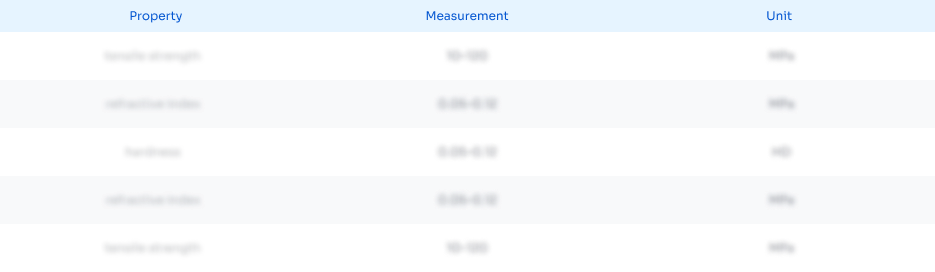
Abstract
Description
Claims
Application Information

- Generate Ideas
- Intellectual Property
- Life Sciences
- Materials
- Tech Scout
- Unparalleled Data Quality
- Higher Quality Content
- 60% Fewer Hallucinations
Browse by: Latest US Patents, China's latest patents, Technical Efficacy Thesaurus, Application Domain, Technology Topic, Popular Technical Reports.
© 2025 PatSnap. All rights reserved.Legal|Privacy policy|Modern Slavery Act Transparency Statement|Sitemap|About US| Contact US: help@patsnap.com