Metal-based composite reinforcement phase casting technique
A technology of metal matrix composite and casting technology, which is applied in the field of metal matrix composite reinforced phase casting technology, which can solve the problems of poor impact resistance, difficult operation, complex bimetal process, etc., and achieve the effect of simple production process and low cost
- Summary
- Abstract
- Description
- Claims
- Application Information
AI Technical Summary
Problems solved by technology
Method used
Image
Examples
Embodiment Construction
[0011] The reinforcing phase material is made into 1-3mm particles and 140 mesh powder, mixed with the binder at a ratio of 1:1:1, the mixed material is filled into the corresponding mold, and then the mixture is dry-pressed with an isostatic press After forming the pellets, it is pre-fired, and the powder and particles of the reinforcing phase are connected to each other through a binder to form a porous structure with high strength, and will not be washed out during the casting of high-temperature molten metal at 1300-1550 °C scattered. The shape, structure and size of the prefabricated body, that is, the core block, can be obtained by designing the corresponding mold. This kind of reinforced phase material powder and granular prefabricated body is more conducive to the casting and infiltration of molten metal, and its thickness can also be adjusted according to the wear resistance requirements of the product. Make adjustments accordingly.
[0012] The casting process of me...
PUM
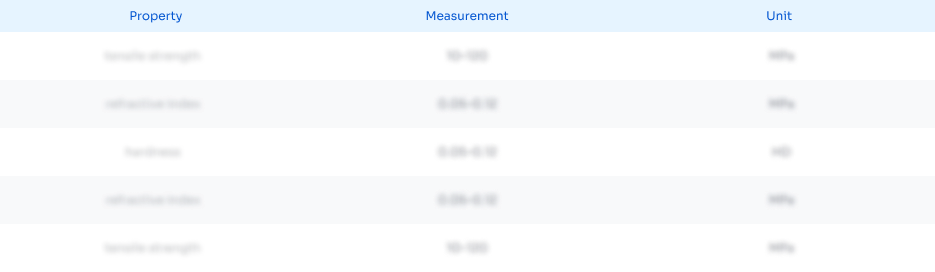
Abstract
Description
Claims
Application Information

- Generate Ideas
- Intellectual Property
- Life Sciences
- Materials
- Tech Scout
- Unparalleled Data Quality
- Higher Quality Content
- 60% Fewer Hallucinations
Browse by: Latest US Patents, China's latest patents, Technical Efficacy Thesaurus, Application Domain, Technology Topic, Popular Technical Reports.
© 2025 PatSnap. All rights reserved.Legal|Privacy policy|Modern Slavery Act Transparency Statement|Sitemap|About US| Contact US: help@patsnap.com