Rotor, and vacuum pump equipped with rotor
A vacuum pump and rotor technology, applied in the direction of pumps, parts of pumping devices for elastic fluids, pump elements, etc., can solve the problem of poor balance workability, application of synthetic resin adhesive M1, and balance workability deterioration. and other problems to achieve the effect of improving exhaust performance
- Summary
- Abstract
- Description
- Claims
- Application Information
AI Technical Summary
Problems solved by technology
Method used
Image
Examples
Embodiment Construction
[0046] Below, while referring to the attached Figure 1 A preferred mode for carrying out the present invention will be described in detail.
[0047] figure 1 (a) is a cross-sectional view of a vacuum pump (screw groove pump parallel flow type) as the first embodiment of the present invention, figure 1 (b) is figure 1 (a) Enlarged view of part B.
[0048] Should figure 1 The vacuum pump P1 in (a) is used, for example, as a gas exhaust mechanism in a processing chamber of a semiconductor manufacturing device, a flat panel display manufacturing device, or a solar panel manufacturing device, or other closed chambers. This vacuum pump has a vane exhaust part Pt for exhausting gas through the rotating vane 13 and a fixed vane 14, a screw groove exhaust part Ps for exhausting gas through the screw grooves 19A and 19B, and their driving system in the outer casing 1. .
[0049] The exterior case 1 has a bottomed cylindrical shape in which a cylindrical pump case 1A and a bot...
PUM
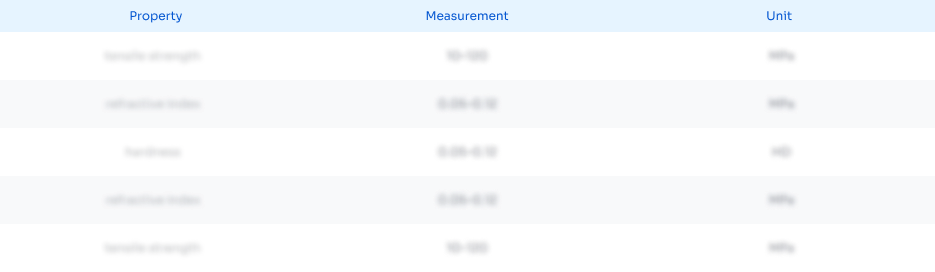
Abstract
Description
Claims
Application Information

- R&D
- Intellectual Property
- Life Sciences
- Materials
- Tech Scout
- Unparalleled Data Quality
- Higher Quality Content
- 60% Fewer Hallucinations
Browse by: Latest US Patents, China's latest patents, Technical Efficacy Thesaurus, Application Domain, Technology Topic, Popular Technical Reports.
© 2025 PatSnap. All rights reserved.Legal|Privacy policy|Modern Slavery Act Transparency Statement|Sitemap|About US| Contact US: help@patsnap.com