Reactive and Disperse Printing Process of Polyester-Cotton Blended Knitted Fabric
A technology of polyester-cotton blending and printing technology, which is applied in the field of active and dispersed same-sizing printing technology of polyester-cotton blended knitted fabrics, can solve the problems of polyester-cotton blended fabrics such as easy yellowing, reduced color brightness, and easy discoloration, and achieves relief. The effect of washing water staining, reducing uneven coloring, and reducing energy consumption for washing
- Summary
- Abstract
- Description
- Claims
- Application Information
AI Technical Summary
Problems solved by technology
Method used
Image
Examples
Embodiment 1
[0045] Printing variety: Polyester / cotton 26S / 1T / C(65 / 35) plain weave (double beaded edge)
[0046] 1 Design the printing pattern: the printing area of the black dot is 22%, the printing area of the red dot is 14%, the printing area of the green dot is 18%, the printing area of the blue dot is 15%, the four-color dot The distribution of is: perfect circle distribution, adjacent color white ground.
[0047] 2 Fabric preparation: Polyester / cotton 26S / 1T / C (65 / 35) plain weave (double bead edge), production network number: S001641R
[0048] Requirements for scouring and bleaching semi-finished products: clean desizing, scouring thoroughly, half-bleaching at will; pH value of the cloth surface is 6-7.5, non-reducible; semi-finished products are evenly dried and wet, without curling, wrinkles, etc.; cloth surface is smooth, Finish is smooth and clean.
[0049] 3 Prepare the original paste, color paste, alkaline paste
[0050] The formula of former paste consists of: 7wt% ...
Embodiment 2
[0080] Printing variety: Polyester / cotton 26S / 1T / C(65 / 35) plain weave (double beaded edge)
[0081] 1 Design the printing pattern: the printing area of dark blue (B1) is 14%, the printing area of bright blue (B2) is 7%, the printing area of light blue (B3) is 9%, and the printing area of lake blue (B4) is 10%, the printing area of light lake blue (B5) is 19%, and the distribution of the five designs is: butterfly distribution, adjacent color white ground.
[0082] 2 Fabric preparation: Polyester / Rayon 20S / 1T / R (65 / 35) plain weave (wick side), production network number: S002591
[0083] Requirements for scouring and bleaching semi-finished products: clean desizing, scouring thoroughly, half-bleaching at will; pH value of the cloth surface is 6-7.5, non-reducible; semi-finished products are evenly dried and wet, without curling, wrinkles, etc.; cloth surface is smooth, Finish is smooth and clean.
[0084] 3 Prepare the original paste, color paste, alkaline paste
[...
Embodiment 3
[0116] Printing variety: Polyester / cotton 20S / 1T / C(65 / 35) plain weave (double beaded edge)
[0117] 1 Design the printing pattern: the printing area of black is 1%, the printing area of light red is 8%, the printing area of dark red is 6%, the printing area of green is 5%, the printing area of blue gray is 11%, and the printing area of light orange is 1%. The printing area is 11%, and the distribution of six colors is: flower distribution, 58% white ground.
[0118] 2 Gray fabric preparation: Polyester / cotton 20S / 1T / C (65 / 35) plain weave (double bead edge) production network number: S001827
[0119] Requirements for scouring and bleaching semi-finished products: clean desizing, scouring thoroughly, half-bleaching at will; pH value of the cloth surface is 6-7.5, non-reducible; semi-finished products are evenly dried and wet, without curling, wrinkles, etc.; cloth surface is smooth, Finish is smooth and clean.
[0120] 3 Prepare the original paste, color paste, alk...
PUM
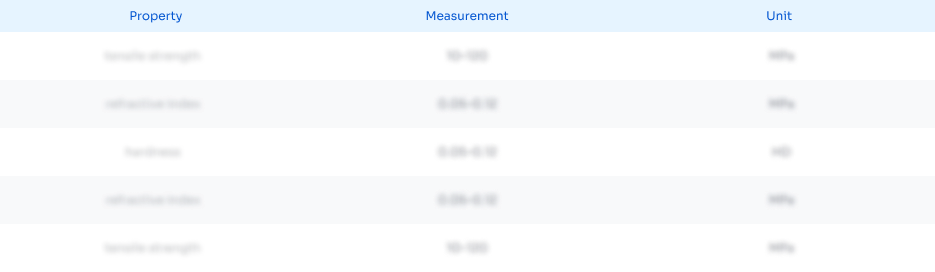
Abstract
Description
Claims
Application Information

- R&D
- Intellectual Property
- Life Sciences
- Materials
- Tech Scout
- Unparalleled Data Quality
- Higher Quality Content
- 60% Fewer Hallucinations
Browse by: Latest US Patents, China's latest patents, Technical Efficacy Thesaurus, Application Domain, Technology Topic, Popular Technical Reports.
© 2025 PatSnap. All rights reserved.Legal|Privacy policy|Modern Slavery Act Transparency Statement|Sitemap|About US| Contact US: help@patsnap.com