Blast furnace iron-making raw material and blast furnace iron-making method
A blast furnace smelting and charging technology, which is applied in the fields of high-aluminum and low-magnesium blast furnace smelting and high-aluminum and low-magnesium blast furnace smelting raw materials, can solve the problems of high cost of blast furnace ironmaking and low smelting performance.
- Summary
- Abstract
- Description
- Claims
- Application Information
AI Technical Summary
Problems solved by technology
Method used
Image
Examples
Embodiment 1
[0037] The blast furnace smelting charge required for blast furnace smelting in this embodiment includes, by weight percentage: 82% of high-alumina and low-magnesium sintered ore, 10% of pellet ore and 8% of raw ore. For the furnace capacity is 3200m 3 blast furnace with 36 tuyeres and an area of 0.4035m2 2 . The kinetic energy of the blast furnace blast is controlled at 155kJ / s, and the air volume is controlled at about 5900m 3 / min, the wind speed control is 285m / s. The blast oxygen enrichment rate is controlled at 2.7%. Blast air temperature is controlled at 1200°C. The heat of molten iron is controlled at 1520°C. The charging system of opening the center and suppressing the edge is adopted. The ore batch weight is 105t, the depth of the material line is 1.4m, and the material speed is 5.5 batches / hour. The tapping time is 100min, the tapping flow rate is 5.8t, and the slag seeing rate is 90%. The mass percentage of pig iron Si is 0.41%, and the slag Al 2 o 3 The...
Embodiment 2
[0045] The blast furnace smelting charge required for blast furnace smelting in this embodiment includes, by weight percentage: 80% of high-alumina and low-magnesium sintered ore, 8% of pellet ore and 12% of raw ore. For the furnace capacity is 3200m 3blast furnace with 36 tuyeres and an area of 0.415m2 2 . The kinetic energy of the blast furnace blast is controlled at 150kJ / s, and the air volume is controlled at about 6050m 3 / min, the wind speed control is 280m / s. The blast oxygen enrichment rate is controlled at 3%. Blast air temperature is controlled at 1200°C. The heat of molten iron is controlled at 1520°C. The charging system of opening the center and suppressing the edge is adopted. The ore batch weight is 110t, the depth of the material line is 1.4m, and the material speed is 5.5 batches / hour. The tapping time is 110min, the tapping flow rate is 6.0t, and the slag seeing rate is 90%. The mass percentage of pig iron Si is 0.41%, and the slag Al 2 o 3 The con...
PUM
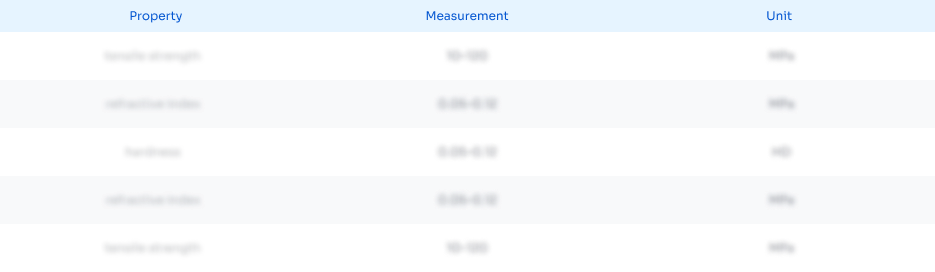
Abstract
Description
Claims
Application Information

- R&D Engineer
- R&D Manager
- IP Professional
- Industry Leading Data Capabilities
- Powerful AI technology
- Patent DNA Extraction
Browse by: Latest US Patents, China's latest patents, Technical Efficacy Thesaurus, Application Domain, Technology Topic, Popular Technical Reports.
© 2024 PatSnap. All rights reserved.Legal|Privacy policy|Modern Slavery Act Transparency Statement|Sitemap|About US| Contact US: help@patsnap.com