Organosilicone packaging glue for packaging LED lamp filament
A LED filament and silicone technology, applied in adhesives, adhesive additives, electrical components, etc., can solve problems such as high viscosity, difficult to degassing, inability to shape, and non-flowing surface, etc., so as to achieve no decrease in light transmittance and strong operability , good leveling effect
- Summary
- Abstract
- Description
- Claims
- Application Information
AI Technical Summary
Problems solved by technology
Method used
Image
Examples
Embodiment 1
[0021] The preparation process of component A is as follows: Weigh 800g of vinyl silicone oil with a viscosity of 3000mpa.s and add it to a 2L vacuum kneader, weigh 200g of fumed silica (wacker N20), and add four times of equal mass to the vinyl silicone oil. After kneading and forming, raise the temperature to 140°C for 2 hours, vacuum for half an hour, the vacuum degree is -0.05Mpa~-0.07Mpa, then lower the temperature and cool down, when the temperature of the glue is cooled below 50°C, add 3g of catalyst platinum-vinylsiloxane (platinum content is 3000ppm), kneading at room temperature for half an hour to obtain the A component;
[0022] The preparation steps of component B are as follows: At room temperature, add 750g of vinyl silicone oil with a viscosity of 3000mpa.s, 50g of crosslinking agent, 20g of adhesive KH570, and 5g of inhibitor ethynyl cyclohexanol into the mixer in sequence, and fill it with nitrogen , mix and stir evenly to obtain the B component.
[0023] Wh...
Embodiment 2
[0025] The preparation process of component A is as follows: Weigh 800g of vinyl silicone oil with a viscosity of 500mpa. In silicone oil, after kneading and molding, heat up to 150°C for 2 hours, vacuum for half an hour, vacuum degree -0.05Mpa~-0.07Mpa, then cool down and cool down, when the temperature of the glue is cooled below 50°C, add 3g of catalyst platinum-vinyl silicon The oxane complex (with a platinum content of 5000ppm) was kneaded at room temperature for half an hour to obtain the A component;
[0026] The preparation steps of component B are as follows: at room temperature, add 750g of vinyl silicone oil with a viscosity of 500mpa.s, 150g of crosslinking agent, 20g of adhesive KH560, and 2g of inhibitor vinyl cyclohexanol into the mixer in sequence, and fill it with nitrogen , mix and stir evenly to obtain the B component.
[0027] When in use, mix the A component and B component uniformly in a weight ratio of 1:1, vacuum defoam for 20 minutes, test the viscosi...
Embodiment 3
[0029] The preparation process of component A is as follows: Weigh 850g of vinyl silicone oil with a viscosity of 15000mpa.s and add it to a 2L vacuum kneader, weigh 147g (wacker N20) fumed silica, add four times of equal mass to the vinyl silicone oil, After kneading and molding, raise the temperature to 145°C for 2 hours, vacuum for half an hour, the vacuum degree is -0.05Mpa~-0.07Mpa, then lower the temperature and cool down, when the temperature of the glue is cooled below 50°C, add 2g of catalyst platinum-vinylsiloxane (Platinum content is 5000ppm), kneading at room temperature for half an hour to obtain the A component;
[0030] The preparation steps of component B are as follows: at room temperature, add 950g of vinyl silicone oil with a viscosity of 15000mpa.s, 145g of crosslinking agent, 50g of adhesive KH570, and 3g of inhibitor vinyl cyclohexanol into the mixer in sequence, and fill it with nitrogen , mix and stir evenly to obtain the B component.
[0031] When in ...
PUM
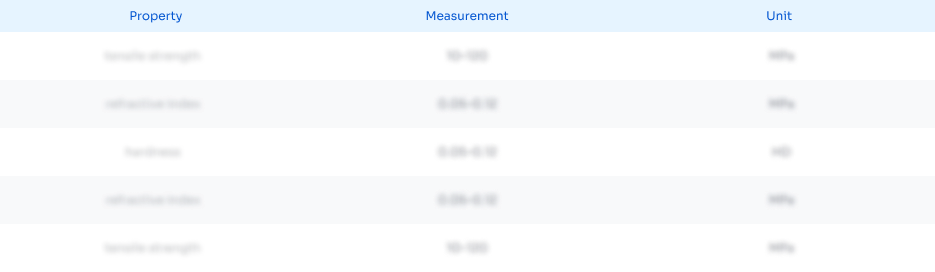
Abstract
Description
Claims
Application Information

- R&D Engineer
- R&D Manager
- IP Professional
- Industry Leading Data Capabilities
- Powerful AI technology
- Patent DNA Extraction
Browse by: Latest US Patents, China's latest patents, Technical Efficacy Thesaurus, Application Domain, Technology Topic, Popular Technical Reports.
© 2024 PatSnap. All rights reserved.Legal|Privacy policy|Modern Slavery Act Transparency Statement|Sitemap|About US| Contact US: help@patsnap.com