Method for determining lifting force and resistance moment of spiral wing
A technique for determining the drag torque and its determination method, which is applied in the field of aircraft control and can solve problems such as large amount of calculation, limited use, and difficult mathematical models
- Summary
- Abstract
- Description
- Claims
- Application Information
AI Technical Summary
Problems solved by technology
Method used
Image
Examples
Embodiment Construction
[0048] Such as figure 1 Shown, the present invention provides a kind of determination method of screw wing lift and drag moment, and the steps are as follows:
[0049] (1) According to the laser three-dimensional imaging stereo method based on the cooperative target, the laser scanning of the spiral wing is carried out to obtain the point cloud of the surface of the spiral wing, as shown in figure 2 and image 3 shown; figure 2 The laser scanning process is described in , the object to be measured is placed on a constant speed turntable that rotates at an angular velocity of Ω, the coordinate axes and the laser position are shown in the figure, and R is the measured value. image 3 In is a schematic diagram of the point cloud obtained after scanning.
[0050] Specifically:
[0051] (1.1) Put the screw wing on the single-axis turntable, and place one of the blades of the screw wing along the angular velocity direction of the single-axis turntable;
[0052] (1.2) Let the ...
PUM
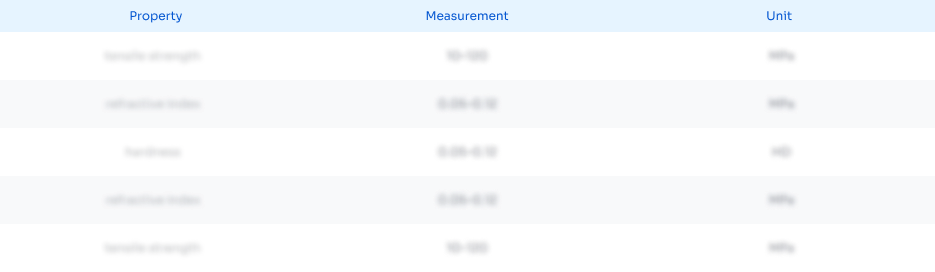
Abstract
Description
Claims
Application Information

- Generate Ideas
- Intellectual Property
- Life Sciences
- Materials
- Tech Scout
- Unparalleled Data Quality
- Higher Quality Content
- 60% Fewer Hallucinations
Browse by: Latest US Patents, China's latest patents, Technical Efficacy Thesaurus, Application Domain, Technology Topic, Popular Technical Reports.
© 2025 PatSnap. All rights reserved.Legal|Privacy policy|Modern Slavery Act Transparency Statement|Sitemap|About US| Contact US: help@patsnap.com