Early strength high wear-resisting self-leveling mortar used for ground repairing and preparation method thereof
A self-leveling mortar and high wear-resistant technology, which is applied in the field of dry powder mortar and its preparation, can solve the problems of poor corrosion resistance, poor wear resistance, and low early strength, and achieve significant economic benefits, social benefits, and good corrosion resistance Effect
- Summary
- Abstract
- Description
- Claims
- Application Information
AI Technical Summary
Problems solved by technology
Method used
Image
Examples
Embodiment 1
[0024] P.052.5 ordinary Portland cement 35kg, mineral admixture 15kg (including heavy calcium powder 10kg, slag powder 5kg), special anti-cracking agent 4kg, imported organic binder 0.5kg, organic defoamer 0.1kg, stable 0.2kg of cellulose, placed in a stirring device and mixed for 5 minutes to obtain a mixture; 0.4kg of high-performance water reducer was slowly and evenly sprayed on the obtained mixture in the form of spraying, and the spraying time was not less than 2 minutes. Stirring is not stopped during the process to ensure that the high-performance water reducer is evenly dispersed in the powder; add 0.3kg of inorganic salt strength accelerator, 45kg of quartz sand (31.5kg of 20-40 mesh, 13.5kg of 40-70 mesh), anti-erosion additive 0.2kg, continue to stir for 10 minutes, make it fully mixed evenly, ready to use, mix well, and stir for 10 minutes, the finished product is obtained.
Embodiment 2
[0026] P.052.5 ordinary Portland cement 35kg, mineral admixture 20kg (including heavy calcium powder 10kg, fly ash 10kg), special anti-cracking agent 6kg, imported organic binder 1kg, organic defoamer 0.2kg, stable 0.4kg of cellulose, placed in a stirring device and mixed for 8 minutes to obtain a mixture; 0.4kg of high-performance water reducer was slowly and evenly sprayed on the obtained mixture in the form of spraying, and the spraying time was not less than 2 minutes. Stirring is not stopped during the process to ensure that the high-performance water reducer is evenly dispersed in the powder; add 0.5kg of inorganic salt strength accelerator, 40kg of corundum (28kg of 20-40 mesh, 12kg of 40-70 mesh), 0.5kg of anti-erosion additive, After continuing to stir for 15 minutes, make it fully mix evenly to obtain the finished product.
Embodiment 3
[0028] P.052.5 ordinary Portland cement 37.5kg, mineral admixture 17.5kg (including heavy calcium powder 10kg, fly ash 7.5kg), special anti-cracking agent 5kg, imported organic binder 0.75kg, organic defoamer 0.15 kg, 0.3 kg of stabilizer cellulose, placed in a stirring device and mixed for 6.5 minutes to obtain a mixture; 0.3 kg of high-performance water reducer was slowly and evenly sprayed on the obtained mixture in the form of spraying, and the spraying time was not less than 2 Minutes, do not stop stirring during the spraying process to ensure that the high-performance water reducer is evenly dispersed in the powder; add 0.4kg of inorganic salt strength accelerator, 20kg of quartz sand (mixed with 20-70 mesh), 20kg of emery (mixed with 20-70 mesh ), 0.35kg of anti-corrosion additive, and continue to stir for 10 to 15 minutes to make it fully mixed evenly to obtain the finished product.
[0029] After testing, the fluidity, early and 28-day strength of the mortar obtained ...
PUM
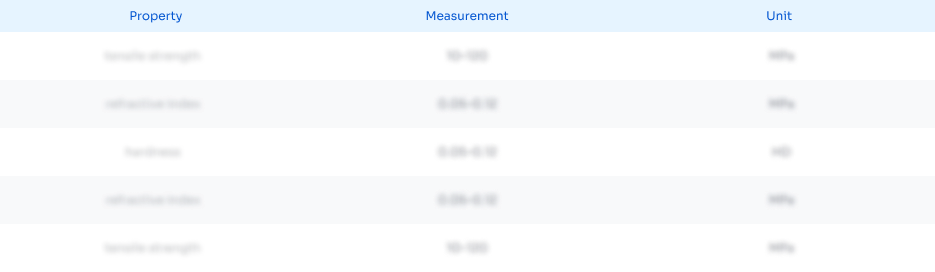
Abstract
Description
Claims
Application Information

- R&D
- Intellectual Property
- Life Sciences
- Materials
- Tech Scout
- Unparalleled Data Quality
- Higher Quality Content
- 60% Fewer Hallucinations
Browse by: Latest US Patents, China's latest patents, Technical Efficacy Thesaurus, Application Domain, Technology Topic, Popular Technical Reports.
© 2025 PatSnap. All rights reserved.Legal|Privacy policy|Modern Slavery Act Transparency Statement|Sitemap|About US| Contact US: help@patsnap.com