Method for recycling waste slag of fused salt chlorination
A technology of molten salt chlorination and recovery method, which is applied in the direction of titanium dioxide, titanium oxide/hydroxide, etc., can solve environmental pressure and other problems, and achieve the effects of saving time and cost, less slag, and simple steps
- Summary
- Abstract
- Description
- Claims
- Application Information
AI Technical Summary
Problems solved by technology
Method used
Image
Examples
preparation example Construction
[0047] The preparation method of artificial rutile usually includes oxidation-reduction to obtain modified raw materials; acid leaching to obtain leaching solution and leaching solid materials; leaching solid materials washing, filtering, drying and high-temperature calcination steps. Adding the regenerated molten salt slag to the acid leaching step can improve the grade of artificial rutile. Further, in order to improve the grade of rutile, as a preferred solution, by mass, the above-mentioned regenerated molten salt slag:modified raw material=20~50:100; more preferably by mass, the above-mentioned regenerated molten salt slag:modified raw material=40 ~50:100.
[0048] Furthermore, the leaching solution obtained in the above acid leaching step can be recycled and treated by using Ruthner waste acid roasting technology to produce regenerated acid and iron powder, which solves the problem of waste acid recycling.
[0049] Further, every time 100g of regenerated molten salt sla...
Embodiment 1
[0062] Embodiment 1 Preparation of regenerated molten salt slag of the present invention
[0063] a. After roughly crushing 1200 molten salt chlorination waste residue with a jaw crusher, ball mill it to -200 mesh ≥ 90%, then mix it with 3600ml of water, stir at room temperature for 1 hour, and filter to obtain filtrate and filter residue;
[0064] b. Recrystallize the filtrate to obtain 1057g of regenerated molten salt residue 1 with a recovery rate of 88.1%; the quality of the residue after drying is 132g.
[0065] The composition and content of the resulting regenerated molten salt slag and filter residue are shown in Table 2:
[0066] Table 2 Composition and percentage of regenerated molten salt slag and filter residue
[0067]
Embodiment 2
[0068] Embodiment 2 Preparation of regenerated molten salt slag of the present invention
[0069] a. After roughly crushing the 600-g molten salt chlorination waste residue with a jaw crusher, ball mill it to -200 mesh ≥ 90%, then mix it with 1800ml of water, stir at room temperature for 1.5h, and filter to obtain filtrate and filter residue;
[0070] b. Recrystallize the filtrate to obtain 535g of regenerated molten salt slag 2 with a recovery rate of 89.2%; the quality of the filter residue after drying is 60g.
[0071] The composition and content of the resulting regenerated molten salt slag and filter residue are shown in Table 3:
[0072] Table 3 Composition and percentage of regenerated molten salt slag and filter residue
[0073]
PUM
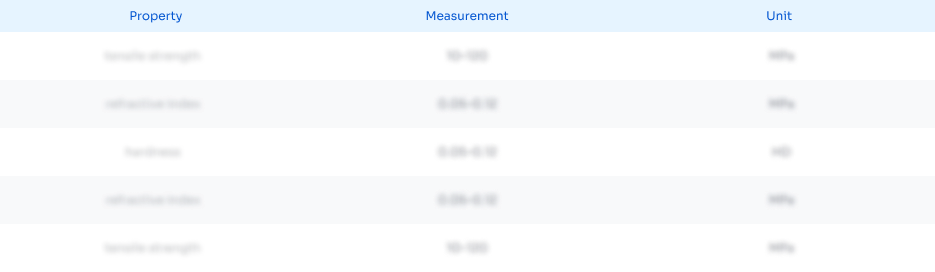
Abstract
Description
Claims
Application Information

- R&D
- Intellectual Property
- Life Sciences
- Materials
- Tech Scout
- Unparalleled Data Quality
- Higher Quality Content
- 60% Fewer Hallucinations
Browse by: Latest US Patents, China's latest patents, Technical Efficacy Thesaurus, Application Domain, Technology Topic, Popular Technical Reports.
© 2025 PatSnap. All rights reserved.Legal|Privacy policy|Modern Slavery Act Transparency Statement|Sitemap|About US| Contact US: help@patsnap.com