A method for preparing high-purity magnesium oxide by utilizing magnesium carbonate coarse ore
A technology of magnesium carbonate coarse ore and magnesium oxide, which is applied to magnesium oxide, reagents, educts, etc., can solve the problems of large resin consumption, high production cost, limited applicable system, etc., and achieves the effect of simple process and convenient operation.
- Summary
- Abstract
- Description
- Claims
- Application Information
AI Technical Summary
Problems solved by technology
Method used
Image
Examples
Embodiment 1
[0034] 1. The raw material is magnesium carbonate coarse ore, which is the primary product of Longmu Co and Jiezechaka salt lake brine (sulphate type and carbonate type salt lake brine), and the main component of the raw material is 67.2% 4MgCO 3 ·Mg(OH) 2 ·5H 2O, the secondary components are NaCl and a small amount of sulfate and 0.27% of boron-containing compounds (calculated as B), etc. First use 80 mesh screens to sieve after magnesium carbonate coarse ore is pulverized, adopt the method for traditional washing, filtration to remove soluble impurity (for example use deionized water to be made into slurry according to the liquid-solid ratio of 5:1 by weight, Filtration in vacuum after mechanical stirring, repeated twice).
[0035] Two, adding mass concentration to the magnesium carbonate coarse ore after screening and removing soluble impurities is 3% sodium carbonate solution as boron removal agent, wherein, calculate according to mass ratio, the liquid-solid ratio of so...
Embodiment 2
[0041] 1. The raw material is magnesium carbonate coarse ore, which is the primary product of Longmu Co and Jiezechaka salt lake brine (sulphate type and carbonate type salt lake brine), and the main component of the raw material is 67.2% 4MgCO 3 ·Mg(OH) 2 ·5H 2 O, the secondary components are NaCl and a small amount of sulfate and 0.27% of boron-containing compounds (calculated as B), etc. First use 60 mesh sieves to sieve after magnesium carbonate coarse ore is pulverized, adopt traditional washing, the method for filtering to remove soluble impurity (for example use deionized water to be made into slurry according to the liquid-solid ratio of 5:1 by weight, Filtration in vacuum after mechanical stirring, repeated twice).
[0042] Two, adding mass concentration to the magnesium carbonate coarse ore after screening and removing soluble impurities is 9% sodium carbonate solution as boron removal agent, wherein, according to mass ratio calculation, the liquid-solid ratio of s...
Embodiment 3
[0048] 1. The raw material is magnesium carbonate coarse ore, which is the primary product of Longmu Co and Jiezechaka salt lake brine (sulphate type and carbonate type salt lake brine), and the main component of the raw material is 67.2% 4MgCO 3 ·Mg(OH) 2 ·5H 2 O, the secondary components are NaCl and a small amount of sulfate and 0.27% of boron-containing compounds (calculated as B), etc. First use 80 mesh screens to sieve after magnesium carbonate coarse ore is pulverized, adopt the method for traditional washing, filtration to remove soluble impurity (for example use deionized water to be made into slurry according to the liquid-solid ratio of 5:1 by weight, Filtration in vacuum after mechanical stirring, repeated twice).
[0049] 2. Add a mixed solution of sodium carbonate and sodium bicarbonate with a mass concentration of 6% to the magnesium carbonate coarse ore that has been screened and remove soluble impurities as a boron removal agent, wherein, calculated accordin...
PUM
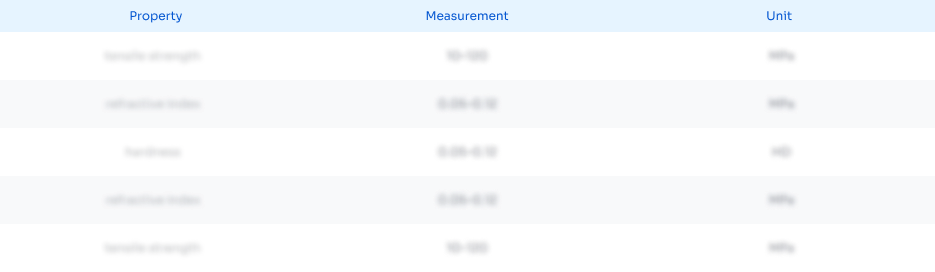
Abstract
Description
Claims
Application Information

- Generate Ideas
- Intellectual Property
- Life Sciences
- Materials
- Tech Scout
- Unparalleled Data Quality
- Higher Quality Content
- 60% Fewer Hallucinations
Browse by: Latest US Patents, China's latest patents, Technical Efficacy Thesaurus, Application Domain, Technology Topic, Popular Technical Reports.
© 2025 PatSnap. All rights reserved.Legal|Privacy policy|Modern Slavery Act Transparency Statement|Sitemap|About US| Contact US: help@patsnap.com