Planar two-degree of freedom robot
A degree of freedom, robot technology, applied in the field of robotics, can solve problems such as inverse solution difficulty, increase motion inertia, slow speed, etc., to achieve the effect of reducing computer requirements and simple control algorithms
- Summary
- Abstract
- Description
- Claims
- Application Information
AI Technical Summary
Problems solved by technology
Method used
Image
Examples
Embodiment Construction
[0019] Attached below figure 1 , attached figure 2 The present invention will be further described.
[0020] as attached figure 1 As shown, the planar two-degree-of-freedom robot includes: a support plate 1, which is arranged above the assembly line, and is set perpendicular to the running direction of the assembly line; servo motor Ⅰ 2 and servo motor Ⅱ 3, which are installed on the support plate 1 Connecting rod I 4, one end of which is fixed on the output shaft of servo motor I 2, and the other end is hingedly installed with the upper end of connecting rod II 5; connecting rod III 6, whose upper end is rotatably fitted on the output shaft of servo motor I 2; Rod IV 7, which is in the shape of a "V", one of its top ends is hingedly installed with the lower end of connecting rod II 5, the other top end is hingedly installed with the upper end of connecting rod V 8, and its bottom end is respectively connected with the lower end of connecting rod III 6 and The upper end of...
PUM
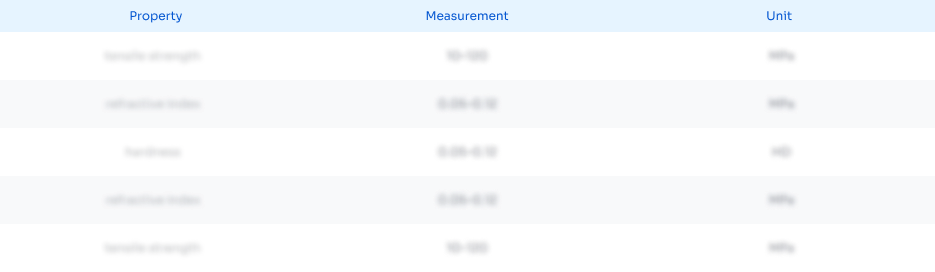
Abstract
Description
Claims
Application Information

- Generate Ideas
- Intellectual Property
- Life Sciences
- Materials
- Tech Scout
- Unparalleled Data Quality
- Higher Quality Content
- 60% Fewer Hallucinations
Browse by: Latest US Patents, China's latest patents, Technical Efficacy Thesaurus, Application Domain, Technology Topic, Popular Technical Reports.
© 2025 PatSnap. All rights reserved.Legal|Privacy policy|Modern Slavery Act Transparency Statement|Sitemap|About US| Contact US: help@patsnap.com