Method and clamp for eliminating deformation of blade caused by machining stress
A technology for processing stress and blades, applied in the direction of manufacturing tools, metal processing equipment, metal processing machinery parts, etc., can solve problems such as blade deformation, and achieve the effect of reducing stress deformation, improving processing efficiency, and eliminating deformation.
- Summary
- Abstract
- Description
- Claims
- Application Information
AI Technical Summary
Problems solved by technology
Method used
Image
Examples
Embodiment Construction
[0008] The present invention is specifically described below in conjunction with accompanying drawing, as figure 1 As shown, the fixture of the present invention includes a hydraulic centering fixture 7, and the hydraulic centering fixture 7 is provided with a cavity one 4, a cavity two 3, and a cavity three 2, and the positioning shaft 5 of the fixture is arranged in the cavity one 4 Inside, the cavity one 4, the cavity two 3, and the cavity three 2 are sequentially connected; the cavity three 2 is provided with an adjusting nut 1, and the adjusting nut 1 can move axially by using the thread on the wall of the cavity three 2; Cavity one 4, cavity two 3, cavity three 2 are filled with liquid plastics.
[0009] In the present invention, the clamping tooling of the positioning shaft of the clamp is designed as a hydraulic centering clamp, and according to the adjustable clamping force of the hydraulic clamp, the critical torque of blade deformation is measured, and the clamping ...
PUM
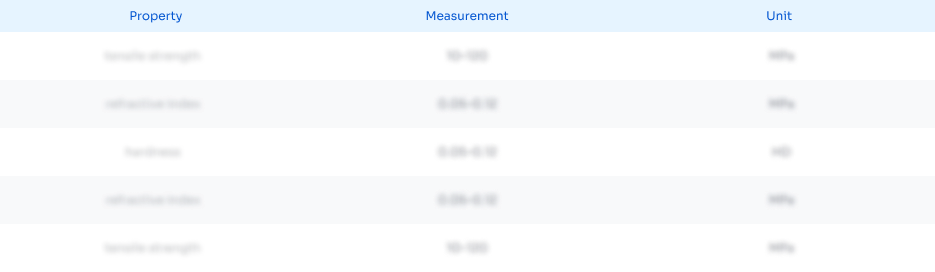
Abstract
Description
Claims
Application Information

- R&D Engineer
- R&D Manager
- IP Professional
- Industry Leading Data Capabilities
- Powerful AI technology
- Patent DNA Extraction
Browse by: Latest US Patents, China's latest patents, Technical Efficacy Thesaurus, Application Domain, Technology Topic, Popular Technical Reports.
© 2024 PatSnap. All rights reserved.Legal|Privacy policy|Modern Slavery Act Transparency Statement|Sitemap|About US| Contact US: help@patsnap.com